身管内表面烧蚀磨损研究进展
0 引言
火炮以自身膛压高、射程远、威力大的特性,在现代陆军武器装备中占有极其重要的地位。随着科技的进步以及提高火炮威力的需要,人们对膛压和发射温度的需求逐渐升高,同时火炮身管的烧蚀也将随之增加。这不仅影响火炮的寿命,同时也会对火炮的射程、精度等性能造成影响。
烧蚀和磨损最早在1886年就被认为是影响身管寿命的重要问题[1],它们会导致身管内径增加、药室增长、膛线变形和内表面破坏[2]等,从而导致炮弹发射时气体逸出,降低了炮弹的速度、射程并增大圆概率偏差。一般来说,当身管直径增加5%时,身管就会报废[3]。而影响身管烧蚀的因素主要有3种:热因素、化学因素和机械因素,这些因素对于烧蚀的贡献有所不同,且相互交织、互相影响,其中热因素是主导因素。因为热因素本身会导致身管内表面低温物质熔化,有严重的烧蚀作用,同时还会促进化学因素的作用。
目前火炮使用Cr-Ni-Mo-V系列钢,该系列钢在经过适当的热加工处理后可满足所身管对力学性能的需要[4],但是耐烧蚀性能远远不足,因此研究身管的烧蚀磨损问题是延长身管寿命的关键问题。
1 烧蚀磨损的产生
膛内燃气温度可达3 000 K、压力可达500 MPa,持续时间大约为十几毫秒[5]。在这种环境下,射管内壁会产生软化、表层组织会发生相变组织退化,甚至化学反应生成的表层低熔点物质会发生熔化。身管内壁极高的加热温度还受到弹带和炮膛内壁摩擦的促进作用,并因为气动加热和不均匀气流而产生局部化。由于烧蚀过程十分复杂,多种因素相互影响,许多学者对于影响烧蚀的3种因素中哪种因素作用最大进行了研究。射击时,身管内壁最高温度可达1 400 K左右[6],在几毫秒后温度下降为大约一半。在膛线初始处所受的热度最高,同时磨损程度也最高。在内表面下不同深度处温度差别很大,0.5 mm深度处的温度通常为420 K[7]。极大的温差导致的温度梯度不但会引起很高的热应力,同时也降低了内表面的硬度。根据发射时气体推动炮弹所产生的动能、身管表面热应力水平和硬度的不同,平均每发炮弹造成的内壁表层烧蚀/磨损厚度在0.1~100 μm。Ahmad[6]认为发射过程中,内膛表面碳化形成的碳化物导致的共晶熔点比炮钢基体低,射击时产生的高速气流会将熔化物冲刷走,造成烧蚀。1975年Montgomery[8]对炮膛与弹带间的相互作用进行了研究,发现即使在静滴实验中铜也会与身管内壁材料发生强烈反应,但在射击的环境下由于反应时间过短二者并无反应,之后通过模拟实验研究烧蚀的产生过程[9],实验得出磨损的机制为熔化-擦除。1984年Montgomery在对前30年间的研究进行了总结和探讨,得出结论:热因素是烧蚀过程中起关键作用的因素[10],在文献中被认为是造成热烧蚀的原因有以下几种:在熔化-擦除过程中,通过推进剂气流中夹带的固体颗粒或者气流本身的机械作用,使身管内表面熔化,表面熔体被冲刷掉。
关于烧蚀磨损导致的身管内表面裂纹,研究重点关注的是裂纹的形成与演变。田桂军[11]将内膛表面的烧蚀磨损过程分为网裂和龟裂2个阶段,根据身管内径的变化量预测火炮的内弹道性能变化量,测算出1 800发后坡膛的磨损量约为50 μm[12]。李洪广[13]总结了烧蚀磨损一般规律,在网裂和龟裂2个阶段中,第一阶段阳线上出现径向裂纹,之后逐渐闭合形成网状裂纹。后一阶段膛线起始部出现气流小溪,裂纹加深,最后膛线被磨平,产生贝壳状龟裂纹[14],严重时有烧蚀坑和冲刷沟。裂纹分张开型 (Ⅰ)、滑开型 (Ⅱ)和撕开型 (Ⅲ)[15]。当身管内径和内表面出现严重损伤时,会导致火炮威力降低,身管寿命也就此终结。
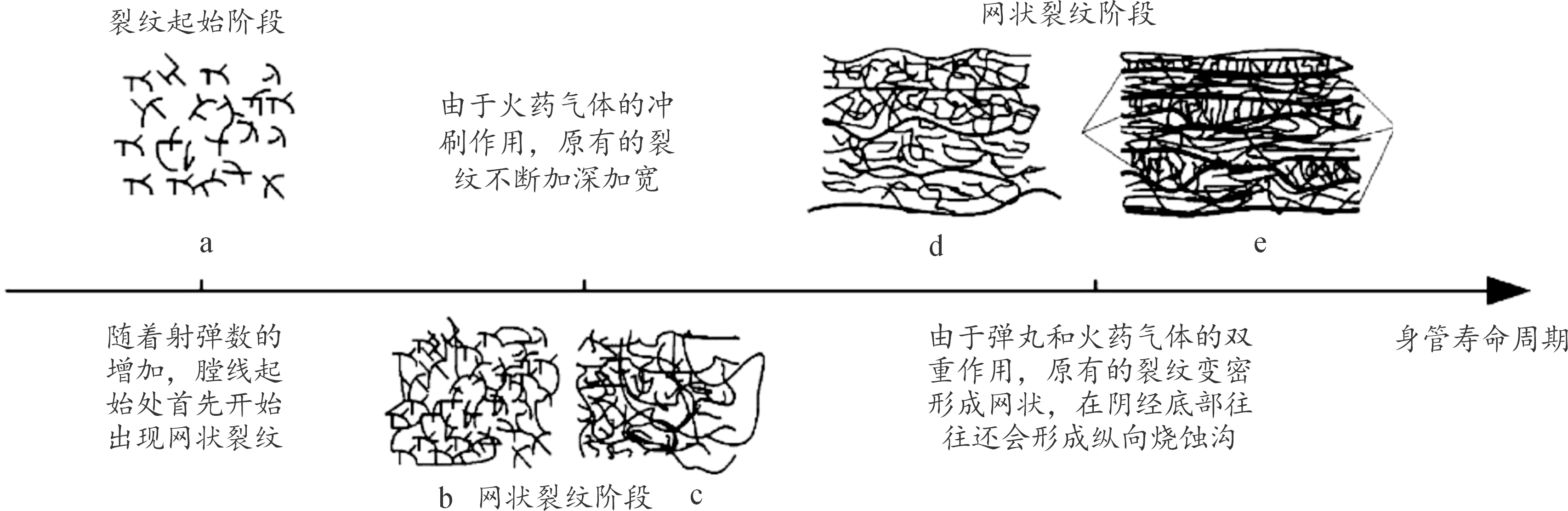
图1 烧蚀磨损过程[16]
Fig.1 The course of erosion
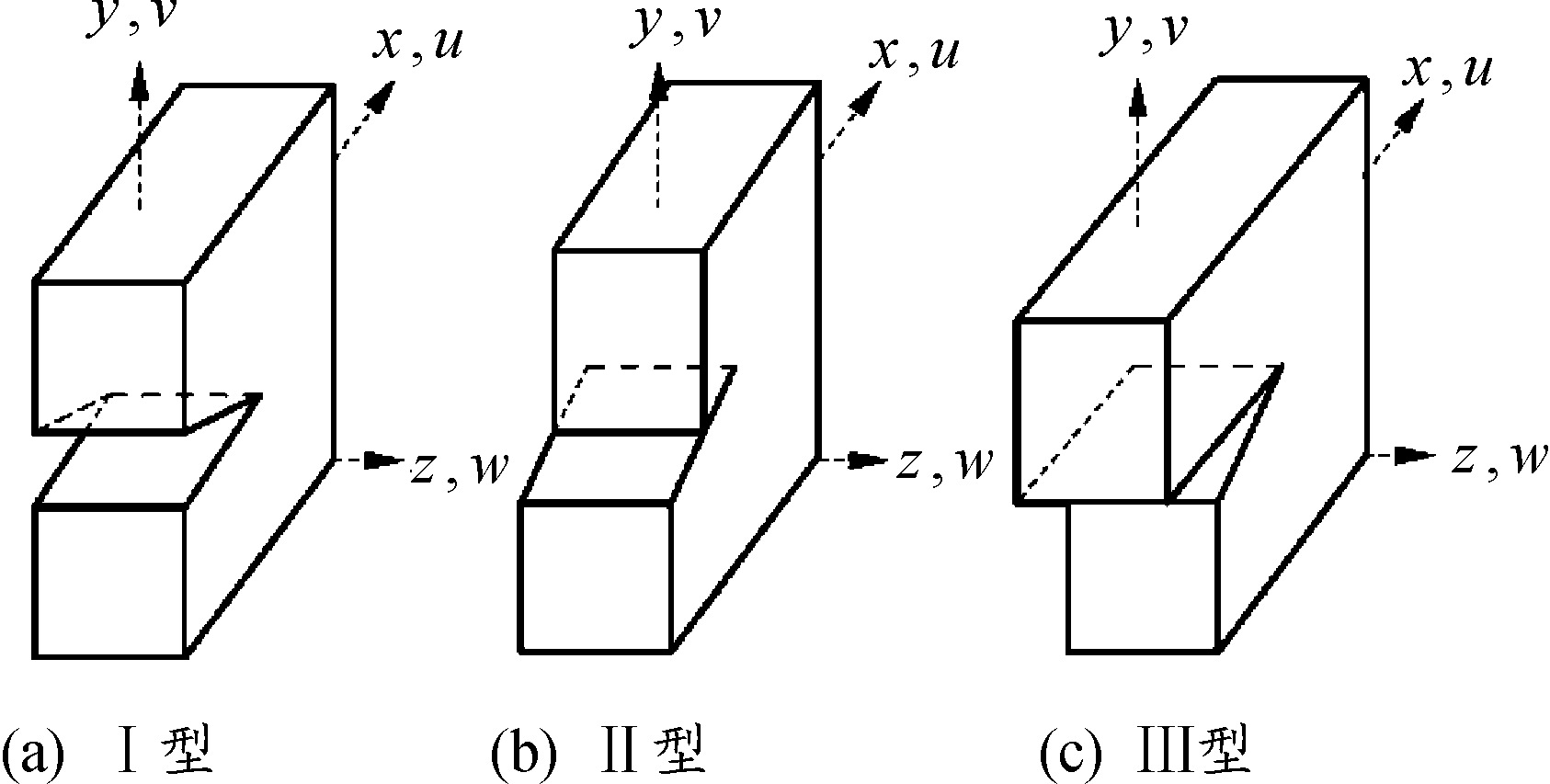
图2 3种典型裂纹形态[17]
Fig.2 Three kind of cracks
2 影响烧蚀磨损的因素
2.1 热因素
推进剂爆燃温度可以在高达3 700 K的温度下产生混合气体[18],热在身管中的主要传播途径是气流的边界层,10%~20%的热量被身管内表面吸收。除了气体的对流之外,弹带对膛线的挤压也会产生大量的热[19]。推进剂从燃烧开始到身管表面的热传递时间跨度仅有20~30 ms,大量的热量通常只积累在身管内壁表面约1 mm以内。气体的温度随着膨胀而降低,因此单纯热因素对身管的烧蚀在身管的初始部分表现最为严重。
为了确认温度这一单独因素对身管烧蚀的影响,Lawton[7]在原始的压力-温度-磨损量关系曲线的基础上又加入了暴露时间这一参数,发现温度对烧蚀的作用是最为显著的。不改变推进剂成分的情况下,对于典型的炮钢,最高膛温Tmax每增加10%,烧蚀增加250%。如果身管内壁温度高于其相变点~750 ℃,则具有体心立方晶格的马氏体会转变为具有面心立方晶格的奥氏体。Paul[20]对身管在一个完整热循环期间产生的体积膨胀进行测量,发现奥氏体相变过程会在750 ℃附近产生体积收缩。加热停止后由于奥氏体(~25×10-6/℃)的热膨胀系数远高于马氏体(~12.5×10-6/℃),从基本无应力的高温条件下快速收缩产生拉伸应力。在燃烧测试中身管内表面温度可达1 127 ℃,表面以下1 mm处最高温度仅为147 ℃[7]。温度差异会产生不同大小的膨胀变形,导致金属表面产生压应力并导致塑性变形。燃烧结束之后,身管内表面表层温度会急剧下降,但内部基体会保持相对较高温度,这会在表面上产生拉伸应力。高低温和拉压应力不断往复循环,最终会导致身管内表面出现微裂纹[21](如图3)。
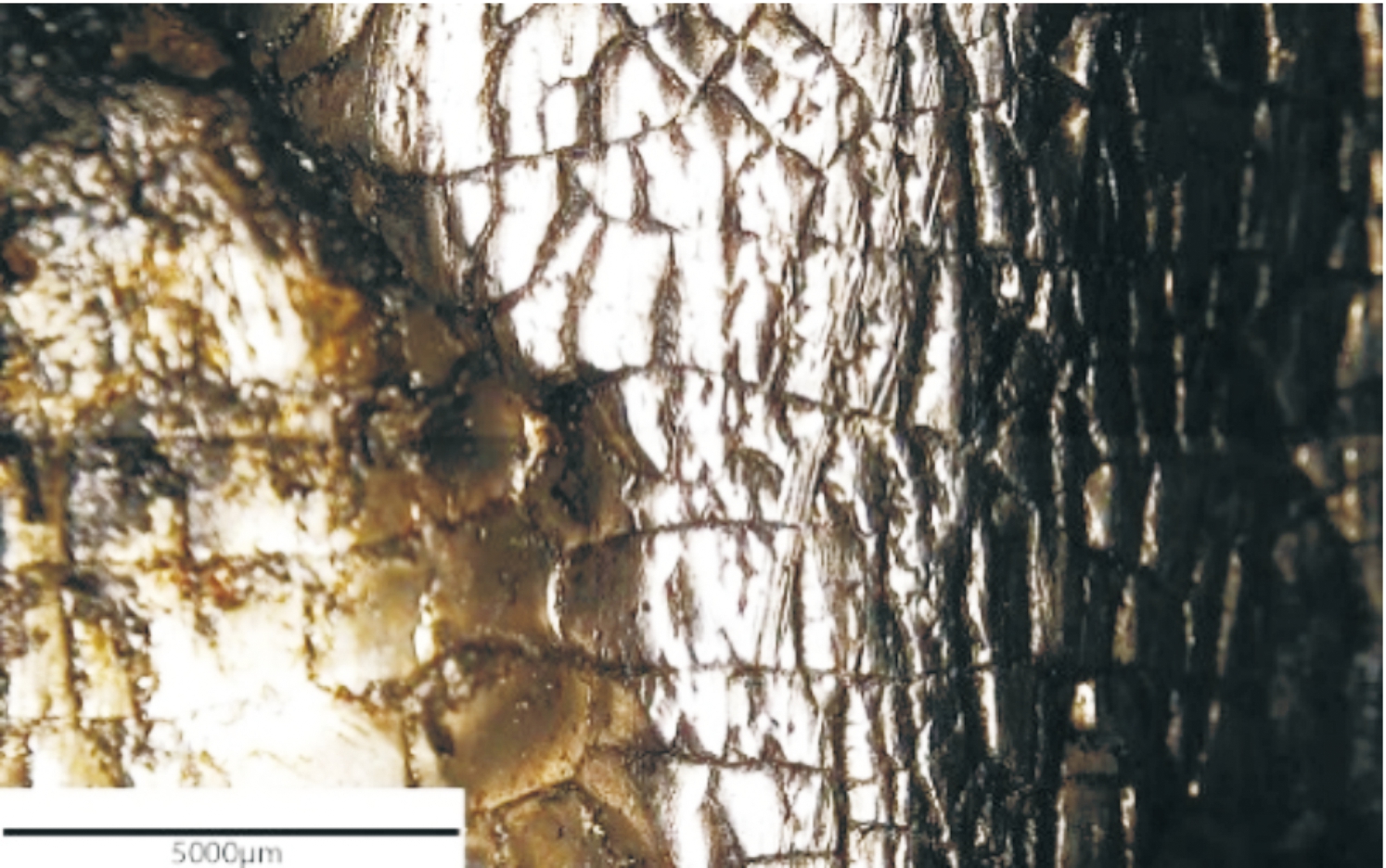
图3 身管内壁上的局部损伤(20倍)
Fig.3 The erosion on inner bore
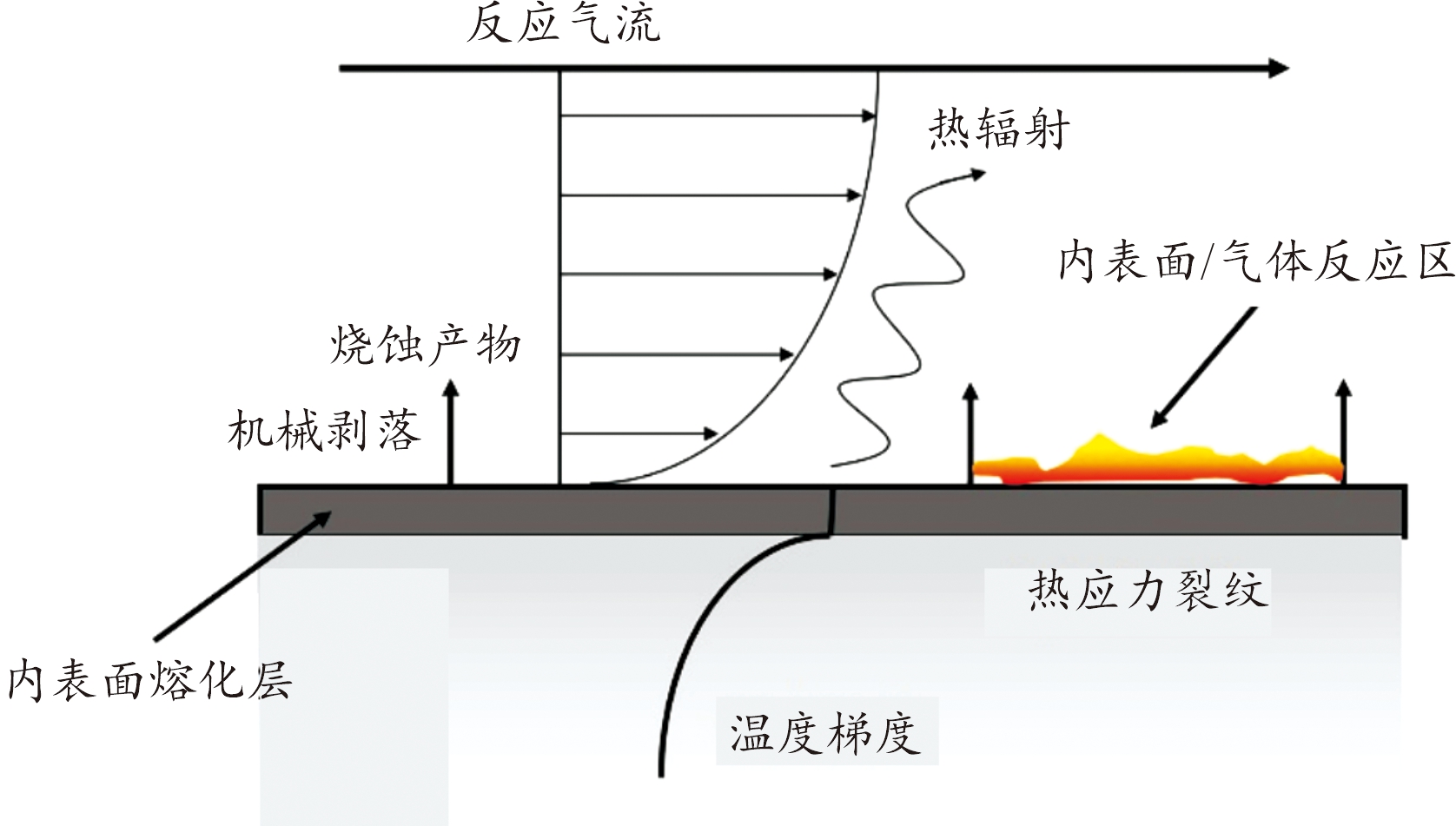
图4 身管热-化学-机械烧蚀作用模型[28]
Fig.4 General schematic of the thermal-chemical-mechanical erosion mechanisms
2.2 化学因素
身管的化学影响区或化学影响层又被称为白层[21-23],深度大概为一至数十微米,通常会被裂纹所贯穿。目前已有研究表明白层影响了化学侵蚀,白层经过加热会导致相变、熔化、裂纹的产生,白层通常由明显的外白层和内白层组成,外白层含有表面化学反应的产物,包括碳化物、氧化物、氮化物、马氏体和残余奥氏体。内白层主要是碳和氮渗入、分布在残余奥氏体和马氏体中。最常提到的化学反应过程包括渗碳、氧化、渗氢,及由此导致的脆化和开裂。
推进剂燃气体有CO、CO2、H2、H2O和N2等5种主要成分和OH、H、O2、O、N、NO等6种还原成分组成[24],知道这些气体每种的侵蚀作用就可以通过改变推进剂组成来降低侵蚀。一些研究人员通过大量的实弹射击结果分析不同气体和侵蚀程度的相关性,同时还有一部分研究人员通过研究理论上的化学反应去推断侵蚀产生的进程。
通过对模拟发射试验的分析,发现了侵蚀和气体种类间的关系。每轮发射的直径烧蚀量可以通过以下公式计算[7]:
ω=Aexp(bTmax)
(1)
式(1)中: Tmax为燃烧期间达到的最高膛温,b为身管内表面硬度相关的常数,A取决于推进剂气体的成分。通过实验数据的多元线性回归得到A的计算式为(以米为单位):
A=exp(0.23fCO2+0.27fCO+0.28fH2O+0.74fH2+
0.16fN2+1.55fR-31.36)
(2)
Lawton[27]提出了2个气体和侵蚀程度相关性的半经验公式,并画出身管内壁化学反应示意图(如图3)。但是Lawton的2个公式并不能解释为什么侵蚀程度依赖于推进剂气体成分。Kimura[21]接着在分析相关关系时假设是由于从气体到身管内表面的传热不同来影响对身管的侵蚀。他将气体组成的热影响和化学影响分开,总结出来不同成分对于侵蚀程度的贡献为:
CO2>CO>H2>H2O>0>N2
因此研究人员发现氮气在化学上具有保护作用,Kimura随后利用这一结果开发了低侵蚀性、高氮含量、不易侵蚀的推进剂。
推进剂产生的侵蚀是由2个不同的过程引起的。首先在高温条件下气体与身管内壁表面产生易反应的、熔点较低的化合物会很快被热和机械过程去除。之后少量气体会在热梯度的驱动下沿径向迅速扩散,从身管内壁表面扩散到身管基体材料中,在身管金属的晶格中形成间隙原子,从而改变钢的晶体结构,影响了身管的物理性能和熔点。这一系列因素使得身管材料的强度降低,脆性增加,更容易受到侵蚀。
大多数研究人员认为大部分的化学侵蚀是由氧化和渗碳导致的,但是也有部分研究人员认为氢是主要的侵蚀气体成分。根据Lawton[7]的相关性实验数据显示,双原子氢是最具侵蚀性的气体。Kimura对此作出的解释是:由于氢气的导热系数比氮气高6倍,因此氢气会传导更多的热量。一些科研人员认为侵蚀是因为氢原子扩散到身管中与碳发生反应,导致脱碳。由于渗碳增加脆性和开裂促进了侵蚀,脱碳又导致身管内壁表面过度软化导致更容易被侵蚀。
2.3 机械因素
高压下反应气体的速度高达800~1 400 m/s[26],这些气体会与固液混合的反应产物以及未完全燃烧的颗粒结合,对身管内表面产生强烈的作用,导致内表面软化甚至熔化。长此以往会使表面金属开始产生裂纹、碎裂,产生的颗粒会被气体裹挟去除[29]。当弹带逐渐挤入膛线坡膛处时会产生数百兆帕的压应力[24,30],旋转的弹丸在阳线的顶部以及导转侧也会产生100~200 MPa的压力,从而产生大量的机械磨损,将阳线磨为圆形、三角形甚至扁平形[31]。
化学反应产生的白层极易被机械侵蚀破坏,而带有镀层的身管容易受到在镀层下松散堆积的氧化物的影响,引起体积膨胀,使表面涂层鼓胀,在发射过程中受到弹带作用被刮除。在发射过程中,推进剂气体通过弹带与膛线间的空隙时会产生喷射,增加了气流的侵蚀程度。这种现象被叫做弹带与膛线之间的气流冲蚀,裂纹的方向也被认为是气流冲蚀存在的重要证据。
机械因素作为其他2种因素的剥落手段,在身管内壁表面发生化学反应或熔化后进行冲刷,增加了内径,对火炮威力和精度造成影响。
3 烧蚀与磨损的保护措施
3.1 镀层
由于热推进剂气体中有许多具有腐蚀性的成分,为了减少气体腐蚀以及隔绝热量,可用铬、钽或者其他材料在身管内表面镀上镀层。Spok[32]绘制了不同镀层发生氧化反应的曲线,发现铬和钽镀层氧化难度大且氧化物熔点高,使基体不容易产生易熔化的氧化物导致磨损。Cote[33]对铬镀层的破坏机制进行了研究,发现使用较高燃烧温度的推进剂时,沿铬和基体间界面的腐蚀会大大破坏铬镀层,因此很少的外力就可以使铬层脱落。燃烧温度更低的推进剂则不容易形成大的镀层烧蚀区域,机械磨损导致的铬疲劳断裂是导致铬层脱落的主要因素。Underwood[34]对3种镀层材料在极端燃烧环境下的热机械磨损进行了观察,并且建立了热损伤模型,发现在炮弹发射过后Ta涂层和SiAlON陶瓷涂层的热裂纹与Cr涂层相似:垂直于身管内壁恒定深度的裂纹,以及平行于身管内壁表面的开裂,导致表面镀层的剥落。这几种不同镀层的区别在于,SiAlON陶瓷镀层的裂纹一开始垂直于表面,后很快转向并平行于表面方向,破坏了更多的镀层材料。Cr和Ta则仅观察到独立的垂直裂纹以及平行裂纹,这两样裂纹结合起来仅仅破坏了少部分表面。由于SiAlON陶瓷具有低导热性,进行有限元计算后得到的身管表面温度最高约为1 900 K。而Cr和Ta涂层最高温度分别为1 250 K和1 400 K,这是因为Ta的热容量低于前者,因此温度更高。
原始的裂纹失效准则适用于Cr和Ta涂层,涂层的预测热膨胀应力与其高温强度的比值在5~10,因此冷却后产生的压缩屈服和拉伸残余应力可能是涂层中垂直裂纹形成的机制。对于SiAlON陶瓷涂层来说这一比值仅为0.6,说明陶瓷的适用破坏机制与其他二者不同。在裂纹产生之后会导致表面镀层的分离,这一剥落机制Cr和Ta相同:被裂纹包围的基体附近的预测剪切应力与其高温抗剪切强度之比在1.6~1.8,也就是镀层会发生烧蚀和剥落现象。对于SiAlON陶瓷来说这一比例为0.6,表明陶瓷镀层的失效机制与金属镀层不同。
镀层对身管内壁有很好的保护作用,虽然制造费用高,但是寿命的提高弥补了这部分的成本。目前最大的问题是如何提高基体与镀层的结合效果,使其不易剥落。
3.2 缓蚀剂
控制烧蚀的关键因素是传热率,如果推进剂的火焰温度较低,则传热率和烧蚀速度会减慢。然而火焰温度低的推进剂提供的动力不足,弹丸的初速度低[35]。于是研究人员在推进剂中添加缓蚀剂,即将导热系数低的无机材料混合到有机相变材料或聚合物中,制成片状或粉末状复合材料后装入推进剂装药结构中[36]。早在20世纪50年代中期,加拿大就发明了聚氨酯泡沫衬套,将它用于105 mm M68坦克炮的脱壳穿甲弹中,身管寿命由100发提高到400发[37]。20世纪60年代,瑞典发明了一种TiO2 -石蜡型人造纤维素内衬,发现它比聚氨酯泡沫衬套有更好的降烧蚀效果。这种缓蚀剂得到迅速推广,成为应用最广泛的标准缓蚀剂。 20世纪70年代初,Picard等研究了滑石粉-石蜡的降烧蚀性能,发现它的降烧蚀效果比TiO2-石蜡优越,但容易形成残渣[13]。为了抑制残渣的产生,我国研究人员研究出稀土缓蚀剂,使镀铬身管使用寿命提升了40%[38]。
Sopok[39]对榴弹炮和坦克炮进行了数值模拟,表明了添加剂对身管的保护性。药室内部分区域的绝热燃烧使双原子氢分解为单原子氢,从而降低了双原子氢的侵蚀。在常用缓蚀剂的基础上,新型缓蚀剂的配方也在不断的研究中。刘波等[40]通过密闭爆发器试验和5.8 mm内弹道实验,对比测试了新型有机硅缓蚀剂801#缓蚀剂的静态燃烧性能和内弹道性能,采用了烧蚀管实验以及氧弹法对比测试了烧蚀性和燃烧完全性。试验结果表明加入5%新型有机硅缓蚀剂与采用相同量801#缓蚀剂相比,前者烧蚀量降低了13.8%具有明显的降烧蚀效果。
由于推进剂的燃烧温度与能量是相对应的,因此很难做到在降低温度减少烧蚀的同时不影响其性能,因此并未得到广泛应用。
3.3 弹带的材质
改进弹带材质与结构设计,对烧蚀也有明显的改善作用。在身管中,弹带主要起到以下作用:(a)增加膛线与弹丸间的压力;(b)阻止弹丸与身管内壁间的气体逸出:(c)当炮身升高时,将弹丸保持在装弹的位置;(d)控制发射时对炮弹的冲击力。在表面之间产生径向压应力时弹带和管壁会在(b)(c)阶段直接参与,以及在(d)阶段参与部分时间。弹丸的外径通常被设计为小于身管膛线内阳线直径,在发射之前弹丸进入坡膛部分,弹带与坡膛接触挤压,使炮弹固定在正确的位置。一旦推进剂被点燃,生成的气体产生足够的压力来克服最初的阻力从而使弹丸发射。因此弹带的径向尺寸会在经过坡膛时逐渐减小直到完全进入膛线部分,这一过程被称为内弹道中弹带的嵌入过程。
在某些弹丸上会有密封带,通常由尼龙或塑料制成位于弹带后方,防止气体从弹丸周围逸出。在身管内有2种相反的力作用于炮弹,一是由高压推进气体推动弹丸底部而产生的推动力,二是弹丸与炮膛之间的摩擦力。
Montgomery[41]研究了弹带表面的熔化过程,认为弹带沿身管滑行的过程应该引入流体动力润滑的过程,摩擦因数应该由薄膜特性决定而不是滑动表面本身的特性决定,并且认为弹带的磨损仅仅取决于发射过程中传递给弹带的热量。Wu[42]研究了嵌入过程中弹带与炮身之间的摩擦磨损,在准静态和动态冲击加载条件下,对铜、铝青铜合金和尼龙弹带进行了嵌入实验,得出以下结论:① 弹带在嵌入过程中会发生摩擦和变形,这说明弹带与身管之间有相互作用。弹带结构(弹带直径和宽度)和炮孔结构(阳线、阴线、坡膛)都对嵌入过程有影响。② 铜、铝青铜合金弹带产生的压力比尼龙弹带高出几个数量级,说明为了匹配现代大口径的炮膛,弹带材料需要经过精心选择。③ 铜弹带在嵌入过程中经过动态冲击加载后的变形行为与弹带在实际燃烧条件下的变形行为非常相似,说明应变速率和温度对于嵌入过程有重要的影响。
4 结论
身管的烧蚀磨损问题与身管的寿命息息相关,一直是火炮发展技术中的难题。目前研究人员对火炮烧蚀的机理进行了深入的研究,得出烧蚀理论模型,并从镀层、弹带设计、火药配比、内膛设计等方面增加内膛的寿命周期,大大提高了身管服役寿命,同时通过内径变化来大致预测身管寿命周期,并且提出裂纹的发展阶段。但是目前的研究还无法得出能够准确预测身管寿命的方法,仅通过检验内膛坡膛处内径的变化量得到的结果较为粗略,因为内膛的烧蚀除了导致内径增大,还会使内径表面形成坑洼不平的沟槽,这也会对炮弹的威力和精度产生影响。目前研究有关身管内裂纹的形貌描述较少,大多从裂纹深度和宽度2个方向进行研究,并没有对裂纹表面的形貌和分布进行观察,仅仅简略的分为起始阶段、扩展阶段和网裂阶段,从这些阶段也无法得出与之对应的身管寿命。
对将来身管研究提出以下几点建议:
1) 在研究内径变化和裂纹径向特征的同时也要同时关注内表面形貌的变化;
2) 寿命预测模型应同时考虑更多因素并将它们结合,同时这些模型应当考虑到相变以及组织演变对身管的影响以及内表面粗糙度对弹丸的影响;
3) 应在进行数值模拟的同时进行对照的模拟实验,并判断未考虑到的因素。
[1] PUTTI A A,CHOPADE M R,CHAUDHARI P E.A review on gun barrel erosion[J].International Journal of Current Engineering and Technology,2011,4(4):231-235.
[2] HU C,ZHANG X.ELSEVIER LTD,Performance variation of a transient dynamic fluid-structure interaction system in different life stages and methods for maintaining the performance[J].Applied Thermal Engineering,2018,130:1012-1021.
[3] 许耀峰,单春来,刘朋科,等.火炮身管寿终机理及寿命预测方法研究综述[J].火炮发射与控制学报,2020,41(3):89-94,101.
XU Yaofeng,SHAN Chunlai,LIU Pengke,et al.Review of the research on failure mechanism and life prediction method of gun barrel[J].Journal of Gun Launch & Control,2020,41(3):89-94,101.
[4] 杨正汉.34CrNi3MoV钢的热处理和性能[J].大型铸锻件,1996(4):31-35.
YANG Zhenghan.Performances and heat treatment of 34CrNi3MoV steel[J].Heavy Casting and Forging,1996(4):31-35.
[5] 付佳维,李延泽,陈诗雨,等.大口径火炮身管损伤机理及寿命提升方法综述[J].装备环境工程,2022,19(7):10-17.
FU Jiawei,LI Yanze,CHEN Shiyu,et al.Erosion mechanisms and life improvement techniques of large calibre gun barrel[J].Equipment Environmental Engineering,2022,19(7):10-17.
[6] AHMAD I,PICARD J.Gun tube erosion and control[C]//Proceedings of the Interservice Technical Meeting.[S.l.]:[s.n.],1970:533.
[7] LAWTON B.Thermo-chemical erosion in gun barrels[J].Wear,2001,250-251(PART 2):827-838.
[8] MONTGOMERY R S.Interaction of copper-containing rotating band metal with gun bores at the environment present in a gun tube[J].Wear,1975,33:109-128.
[9] MONTGOMERY R S.Friction and wear at high sliding speeds[J].Wear,1976,36(3):275-298.
[10] MONTGOMERY R S.Wear of projectile rotating bands[J].Wear,1985,101(4):347-356.
[11] 田桂军.内膛烧蚀磨损及其对内弹道性能影响的研究[D].南京:南京理工大学,2003.
TIAN Guijun.Researches on the wear and erosion of bore and its influence to interior ballistic performance[D].Nanjing:Nanjing University of Science and Technology,2003.
[12] MONTGOMERY R S,SAUTTER F K,ARMAMENT U S A,et al.A review of recent american work on gun erosion and its control[J].Wear,1984,94:193-199.
[13] LI H,YAN J,SHIGUO D,HAIPING C.Research advance of erosion inhibitor technology in gun barrel[J].Gun Launch and Control,2012:103-106.
[14] 韦丁,王琼林,严文荣.降低身管烧蚀性研究进展[J].火炸药学报,2020,43(4):351-361.
WEI Ding,WANG Qionglin,YAN Wenrong.Research progress on reducing erosivity of gun barrel[J].Chinese Journal of Explosives & Propellants,2020(4):351-361.
[15] ZENG Z Y,MA M DI,NING B F,GAO X K.Analysis of rifling land damage mechanism of gun barrel[J].Acta Armamentarii,2014,35(11):1736-1742.
[16] 张金.火炮身管内膛损伤机理分析[J].火力与指挥控制,2020,45(5):8-14.
ZHANG Jin.Mechanism analysis of internal defects in barrels[J].Fire Control & Command Control,2020,45(5):8-14.
[17] 刘朋科,杨雕,王军,等.身管材料烧蚀磨损性能研究[J].火炮发射与控制学报,2021,42(4):28-33.
LIU Pengke,YANG Diao,WANG Jun,et al.Study on ablation and wear properties of barrel materials[J].Journal of Gun Launch & Control,2021,42(4):28-33.
[18] 龚长红,杨云飞,黄林昊.现代火炮炮膛烧蚀磨损机理及控制措施[J].四川兵工学报,2014,35(11):127-129.
GONG Changhong,YANG Yunfei,HUANG Linhao.Modern artillery bore erosion wear mechanism and control measures[J].Journal of Sichuan Ordnance,2014,35(11):127-129.
[19] YUAN D,ZHOU G,LI X.Simulation study on rifling stress in the process of bullet engraving into barrel[J].Journal of Ordnance Equipment Engineering,2020,41(8):30-35.
[20] COTE P J,LEE S L,TODARO M E,et al.Application of laser pulse heating to simulate thermomechanical damage at gun bore surfaces[J].Journal of Pressure Vessel Technology,Transactions of the ASME,2003,125(3):335-341.
[21] ENTÜRK A,I
K H,EVCI C.Thermo-mechanically coupled thermal and stress analysis of interior ballistics problem[J].International Journal of Thermal Sciences,2016,104:39-53.
[22] MONTGOMERY R S.Muzzle wear of cannon[J].Wear,1975,33(2):359-368.
[23] UNDERWOOD J H,PARKER A P,COTE P J,et al.Compressive thermal yielding leading to hydrogen cracking in a fired cannon[J].Journal of Pressure Vessel Technology,Transactions of the ASME,1999,121(1):116-120.
[24] JOHNSTON I A.Understanding and predicting gun barrel erosion[J].Understanding &Predicting Gun Barrel Erosion,2005:48.
[25] SHERRICK K.Corrosion-and erosion-based materials selection for the m242 autocannon barrel in a marine operating environment[D].MA Dissertation,Rensselaer Polytechnic Institute,2012.
[26] 冯国铜.镀铬枪管带泄漏的膛内流场与管壁温度场研究[D].南京:南京理工大学,2018.
FENG Guotong.Study on flow field with gas leakage and temperature field of chromiun-plating barrel[D].Nanjing:Nanjing University of Science and Technology,2018.
[27] LAWTON B.The influence of additives on the temperature,heat transfer,wear,fatigue life,and self ignition characteristics of a 155 mm gun[J].Journal of Pressure Vessel Technology,Transactions of the ASME,2003,125(3):315-320.
[28] SOPOK S,RICKARD C,DUNN S.Thermal-chemical-mechanical gun bore erosion of an advanced artillery system part one:Theories and mechanisms[J].Wear,2005,258(1-4 SPEC.ISS.):659-670.
[29] 易怀军.火炮身管烧蚀磨损的影响研究[D].南京:南京理工大学,2016.
YI Huaijun.Study on influence of gun barrel ablation wear[D].Nanjing:Nanjing University of Science and Technology,2016.
[30] 石立雄.枪管寿命技术研究[D].南京:南京理工大学,2016.
SHI Lixiong.Research on barrel life technology[D].Nanjing:Nanjing University of Science and Technology,2016.
[31] SHEN C,ZHOU K,LU Y,et al.Modeling and simulation of bullet-barrel interaction process for the damaged gun barrel[J].Defence Technology,2019,15(6):972-986.
[32] SOPOK S,O’HARA P,PFLEGL G,et al.American Institute of Aeronautics and Astronautics,1997.Thermochemical erosion modeling of the 25 mm M242/M791 gun system[C]//33rd Joint Propulsion Conference and Exhibit.1997 Reston,Virigina:32.
[33] UNDERWOOD J H,PARKER A P,VIGILANTE G N,et al.Thermal damage,cracking and rapid erosion of cannon bore coatings[J].Journal of Pressure Vessel Technology,Transactions of the ASME,2003,125(3):299-304.
[34] UNDERWOOD J H,VIGILANTE G N,MULLIGAN C P.Review of thermo-mechanical cracking and wear mechanisms in large caliber guns[J].Wear,2007,263(7-12 SPEC.ISS.):1616-1621.
[35] DAHIWALE S M,BHONGALE C,ROY S,et al.Studies on ballistic parameters of di-butyl phthalate-coated triple base propellant used in large caliber artillery gun ammunition[J].Journal of Energetic Materials,2019,37(1):98-109.
[36] 孙娜.有机—无机纳米复合材料的制备、性能及其在含能材料中的应用研究[D].南京:南京理工大学,2018.
SUN Na.Preparation and properties of organic-inorganic nanocomposites and their applications in energetic materials[D].Nanjing:Nanjing University of Science and Technology,2018.
[37] 李炳生,任英良.炮管降烧蚀添加剂的研究动态及前景[J].兵器材料科学与工程,1991(1):25-30.
LI Bingsheng,REN Yingliang.Research trend and prospect of anti-ablation additives for gun barrel[J].Journal of Sichuan Ordnance,1991(1):25-30.
[38] 樊伟,崔艳芳,田甜,等.稀土氧化物作为缓蚀添加剂隔热机理研究[J].兵器材料科学与工程,2014,35(11):127-129.
FAN Wei,CUI Yanfang,TIAN Tian.Thermal insulation mechanism of rare earth oxides as erosion reducing additive[J].Ordnance Material Science and Engineering,2014,35(11):127-129.
[39] SOPOK S,RICKARD C,DUNN S.Thermal-chemical-mechanical gun bore erosion of an advanced artillery system part two:Modeling and predictions[J].Wear,2005,258(1/4):671-683.
[40] 郑双,刘波,刘少武.新型有机硅降蚀剂在小口径武器装药中的应用[J].含能材料,2011:335-338.
ZHENG Shuang,LIU Bo,LIU Shaowu.Application of a new agent of low erosion in the small caliber weapon[J].Chinese Journal of Energetic Materials,2011:335-338.
[41] MONTGOMERY R S.Surface melting of rotating bands[J].Wear,1976,38(2):235-243.
[42] WU B,ZHENG J,TIAN Q T,et al.Elsevier,friction and wear between rotating band and gun barrel during engraving process[J].Wear,2014,318(1/2):106-113.