____________________________________________________________________________________________________________________________________
引用格式:吕鹏博,王伟力,刘晓夏,等.含裂纹装药缺陷的侵爆战斗部穿甲过程装药安定性的数值模拟研究[J].兵器装备工程学报,2017(11):26-30.
Citation formatLYU Pengbo, WANG Weili, LIU Xiaoxia, et al.Research on Numerical Simulation of Stability of the Charge of Invasion of Explosive Warheads Containing Seam Defects in Armor-Piercing Process[J].Journal of Ordnance Equipment Engineering,2017(11):26-30.
____________________________________________________________________________________________________________________________________作者简介:吕鹏博(1992—),男,硕士研究生,主要从事战斗部装药安定性研究。
____________________________________________________________________________________________________________________________________
含裂纹装药缺陷的侵爆战斗部穿甲过程装药安定性的数值模拟研究
摘要:为了分析含不同因素的裂纹装药缺陷的侵爆战斗部在侵彻过程中装药安定性的问题,利用正交试验建立了含9种裂纹缺陷的装药、弹体和靶板模型,并利用ANSYS/LS-DYNA模拟了在侵彻靶板时缺陷在冲击载荷作用下的塑性变形情况,计算了炸药的应变能和热分解作用下装药的局部温升情况,从温度角度对含缺陷战斗部的装药安定性进行了分析。模拟分析了裂纹缺陷四个因素对于侵爆战斗部装药的侵彻安定性影响主次,得出了位于卵头部装药区的圆柱状裂纹缺陷对于含缺陷的战斗部装药的安定性影响较大的结论。
关键词:装药缺陷;装药安定性;塑性应变能;穿甲
中图分类号:TJ410.1 文献标识码:A 文章编号:2096-2304(2017)11-0026-05
Research on Numerical Simulation of Stability of the Chargeof Invasion of Explosive Warheads Containing Seam Defectsin Armor-Piercing Process
Abstract: To study the influencing of the charge safety which has seam defects armor-piercing process during the armor-piercing process in this paper, we have created the annular shaped about warhead which has munitions flaw and the target. We have simulated the process of penetrating. And we calculated the temperature variation in some area about the above process, and we have get some conclusion about the charge safety based on the above data. It is concluded that the cylindrical crack defects in the filling area of the egg head are influential to the stability of the defective warhead after seam defects through numerical simulation research under the four factors three levels for the invasion of explosive warhead charge penetration stability.
Key words: charge defects; charge safety; plastic strain energy; armour piercing
当前我国社会环境繁荣稳定,军方列装的导弹武器装备有很大可能在全寿命周期内都会处于贮藏或战备训练状态,在此期间,导弹战斗部装药不可避免地会受到温度、振动,湿度等外界环境条件变化的刺激,这将使得战斗部内部装药产生一些物理、化学变化,在战斗部内部装药中形成孔洞和裂纹状装药缺陷[1]。而侵爆战斗部在侵彻目标防护时,弹体要承受超过10 kg的过载[2],如此高的过载传进侵爆战斗部内部装药中,会使装药缺陷发生塌缩、闭合摩擦等,进而对侵爆战斗部内部装药的安定性产生影响。因此,分析含装药缺陷的侵爆战斗部在侵彻过程中装药安定性问题,对于延长侵爆战斗部使用寿命以及战斗部生产工艺水平发展有一定意义。
国内学者对此进行了大量研究,石海啸、戴开达[3]数值模拟了战斗部侵彻过程中PBX动态损伤,得出了在侵彻过程中最大裂纹出现在头部和中部区域的结论,实际最大裂纹宽度超过1.2 mm,这表明战斗部在侵彻过程中,装药对于应力波的响应主要集中在头部和中部区域。赵勇华、陈霜艳[2]等研究了侵彻战斗部在侵彻混凝土靶板过程中,在着靶冲击波和摩擦作用下,无缺陷装药的侵彻战斗部侵彻过程中装药温升最大为400 K左右。另外王洪波,刘群、尚海林等[4~8]研究了 PBX炸药细观孔洞缺陷对其冲击点火特性的影响,研究表明细观孔洞对于外界的载荷有良好的响应,PBX炸药的温升比较明显。焦志刚、郭秋萍[9]利用炸药临界起爆压力公式研究了半穿甲弹侵彻过程中装药安定性发现弹丸侵彻25 mm均质钢会发生早炸。以上多是对于完整弹药的装药安定性展开研究,或者细观结构下PBX炸药的冲击点火机理的研究,对于装药存在缺陷的战斗部在侵彻过程中安定性的研究还比较少,需要进一步的研究探索。
1 有限元模型的建立
1.1 战斗部模型的建立
研究对象选用典型侵爆战斗部,该型战斗部由卵形头部和圆柱体弹身组成,弹身长650 mm,底部直径250 mm,壳体厚度为12 mm。该战斗部的壳体为高强度材料30CrMnSi2A,装药为某含铝PBX炸药(75.5%的RDX、20%的铝粉和4.5%的粘结剂),靶板材料为某船用钢。考虑到模型的对称性,在数值模拟过程中对战斗部和靶板物理模型采用1/2等尺寸模型(为简化模型和减少数值模拟的运算量,将战斗部内引信部位换为主装药)。具体物理模型如图1所示。
1.2 裂纹装药缺陷有限元模型的建立
侵爆战斗部内部装药的缺陷大致可以分为孔洞和裂纹缺陷两类,本研究主要针对裂纹缺陷[10]。在外界条件下形成弹体装药裂纹缺陷具有随机性,假设战斗部内部裂纹装药缺陷有形状、尺寸大小、轴向位置和缺陷姿态四个影响因素,且四个因素对于装药安定性的影响相互独立,利用四因素三水平的L9(34)正交试验表头设计数值模拟工况,通过数值模拟就可得出裂纹缺陷四因素对于含裂纹装药缺陷的侵爆战斗部在穿甲过程中装药安定性的影响主次。表1给出了这四个因素的三个水平设置情况。
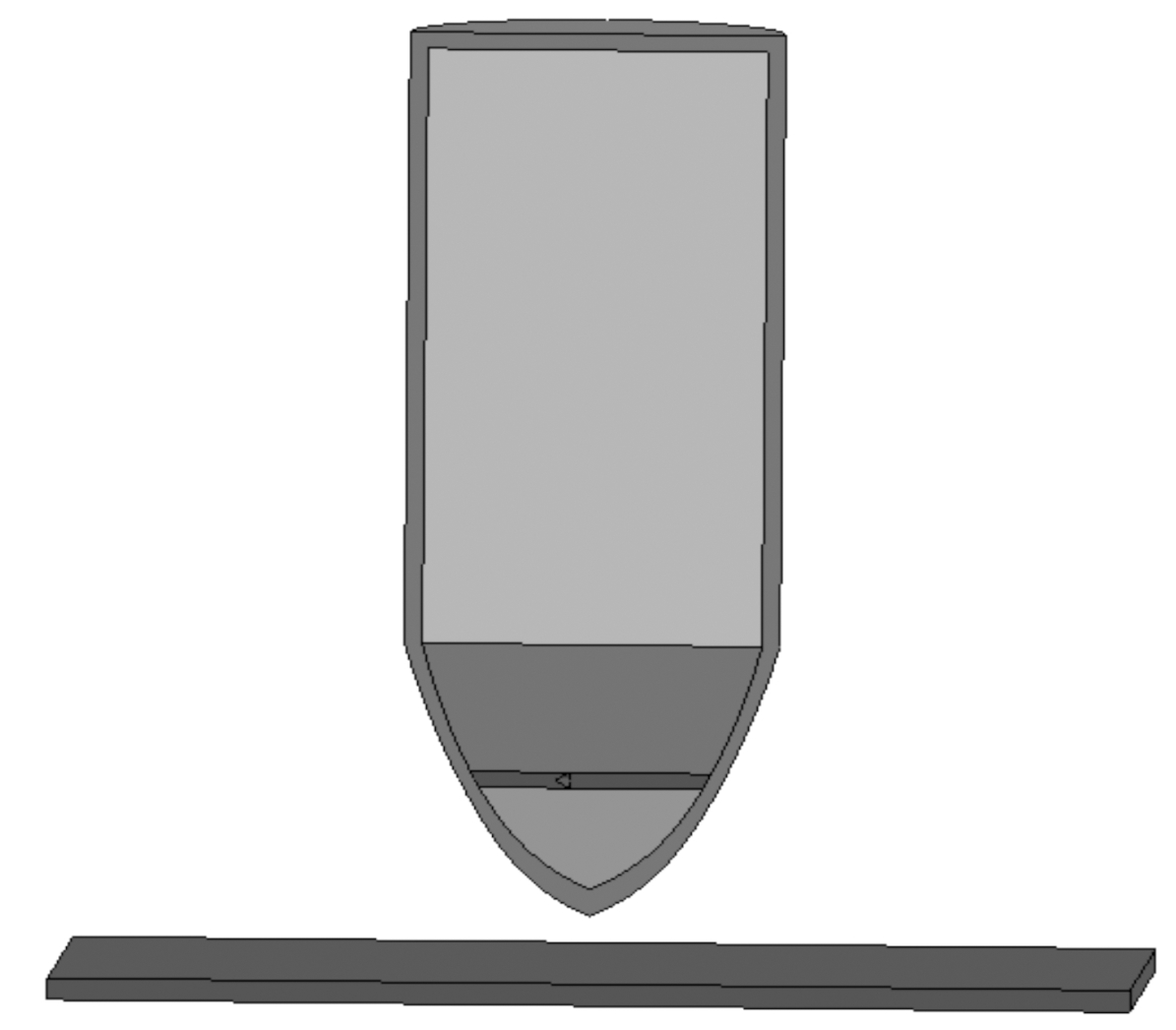
图1 战斗部和靶板物理模型
表1 裂纹装药缺陷的影响因素水平 mm
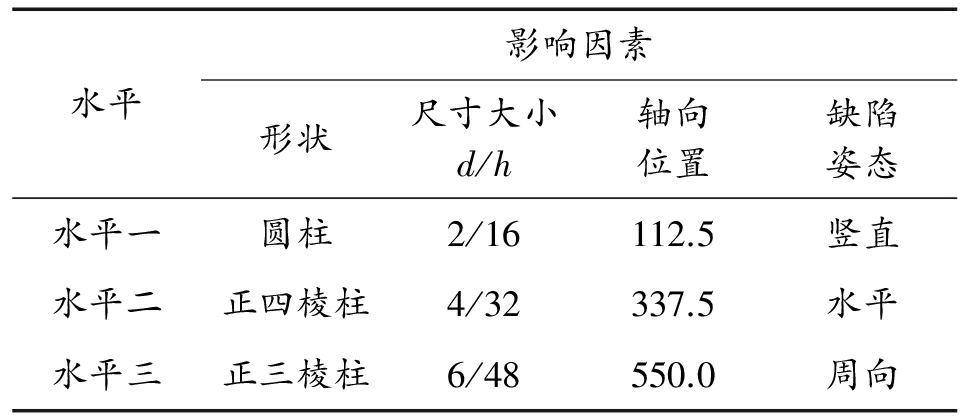
注:d表示柱底面直径或边长,h表示柱高。
表2为正交试验表。设计的含裂纹装药缺陷的侵爆战斗部物理模型,设裂纹处为真空。在有限元模型建立过程中对外壳、装药界面采用共节点处理。为保证计算精度,在装药存在缺陷部位进行网格加密处理。
表2 裂纹缺陷影响因素正交试验表 mm
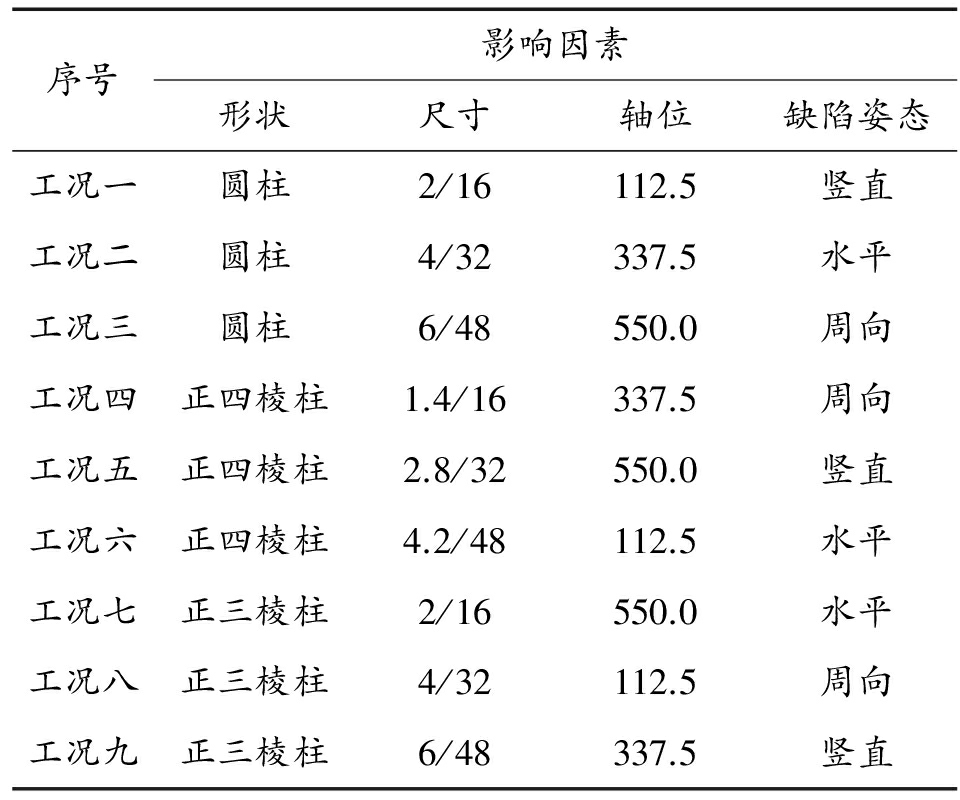
1.3 有限元模型的本构关系
李尚昆[12]根据高聚物黏结炸药的力学性能进行的SHPB实验和动态巴西圆盘实验,得出PBX炸药具有明显的拉压不对称性。根据侵彻过程中装药实际受载条件,在数值模拟时采用装药压缩条件下的力学性能参数,选用各项同性的弹塑性材料本构模型,侵爆战斗部的壳体和靶板采用弹塑性随动强化材料模型。具体参数[2,11-12]如表3所示。
表3 数值模拟各材料的力学性能参数
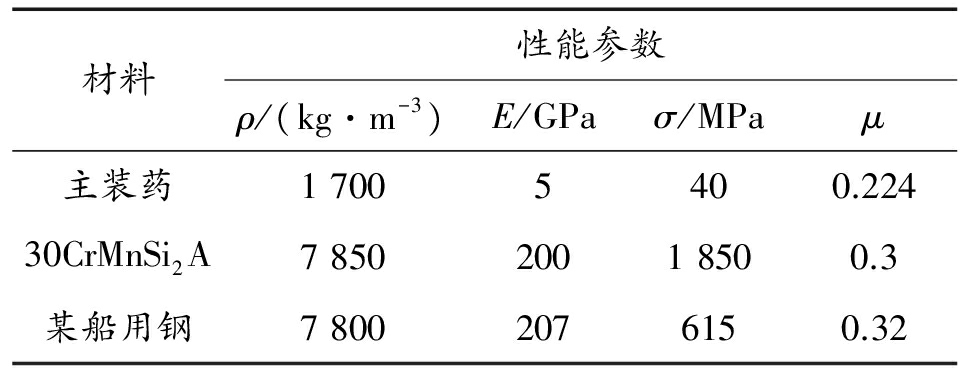
2 含缺陷的局部装药温升的假设与计算
根据炸药非冲击起爆的“热点”学说,装药的安定性可从装药的温度进行考量。侵爆战斗部装药在应力波作用下会产生较大的塑性应变,塑性应变能积累使得炸药发生局部温升。假设数值模拟中装药缺陷处装药单元的塑性变形所做的塑性应变能全部转化为内能。另外,考虑到该侵爆战斗部主装药成分主要为RDX和铝粉,根据炸药配比可以推算出单位质量。该PBX炸药的放热量ΔH,而其中RDX的热分解可用Arrhenius方程描述,并计算出主装药反应过程中放出的热量。
忽略侵爆战斗部穿甲过程中装药热量的耗散,将LS-DYNA解算结果利用Matlab编程计算出装药单元在每个时间步装药反应释放的热量Qi和塑性应变能Wsi共同作用下的温度,从而判断装药的热安定性。
Ti+1=+
+Ti=
+
+Ti
(1)
式(1)中: σi和Δεi分别代表装药单元在LS-DYNA解算时每个时步的应力和有效塑性应变增量; Ti为炸药单元i时步的温度(K); ρ为RDX的密度1 700 kg/m3; CV为RDX的热容1 330 J/(kg·K), ΔH代表该配比的PBX热分解反应热7.3E+6 J/kg; Z代表RDX热分解反应的指前因子为1E+16(1/s); Ea代表RDX受热发生反应的活化能180 kJ/mol; R代表普适气体常数8.314 J/(K·mol)。设定环境参考温度取300 K,即T0=300 K。
3 含裂纹装药缺陷的侵爆战斗部穿甲过程的数值模拟分析
3.1 基于正交试验设计工况的数值模拟分析
根据前面利用L9(34)正交试验表设计的第三、五和七组含裂纹装药缺陷的侵爆战斗部以1.5倍音速(510 m/s)垂直侵彻16 mm厚船用钢靶后,含裂纹装药缺陷的局部主装药的应变云图如图2。从图2可以看出:① 裂纹装药缺陷的形状、尺寸、轴向位置和水平位置这四个因素对于侵爆战斗部穿甲过程中的装药安定性影响比较显著,不同形状、尺寸以及位置的裂纹缺陷均在缺陷处形成较大的塑性应变(相较于远离裂纹缺陷的区域)。这表明无论裂纹装药缺陷的形状和位置等因素如何变化,缺陷处装药都会发生应力集中,进而表现为该处装药形成较大的塑性应变。② 发生较大塑形应变的装药单元主要集中在裂纹装药缺陷某些特定位置并呈现一定的规律性。例如正四棱柱状裂纹缺陷发生较大塑性变形的单元就集中在棱柱端面正方形的棱、角附近,圆柱状裂纹缺陷发生较大塑性变形的单元就集中在圆柱截面及附近曲面上,而正三棱柱状裂纹缺陷发生较大塑性变形的单元就集中在三棱柱侧面棱边以及附近的装药单元上。③ 观察工况三、五和七装药缺陷处装药单元的应变云图可以发现,裂纹缺陷处于侵爆战斗部头部区域时,装药单元形成的塑性应变都比较大,这表明存在于侵爆战斗部头部区域的裂纹装药缺陷对于战斗部侵彻过程中形成的应力波的响应最明显,该处装药单元所形成的有效塑性应变也就越大,但是侵爆战斗部以1.5倍音速侵彻靶板过程中,装药裂纹发生的有效塑性变形并未使裂纹发生闭合。
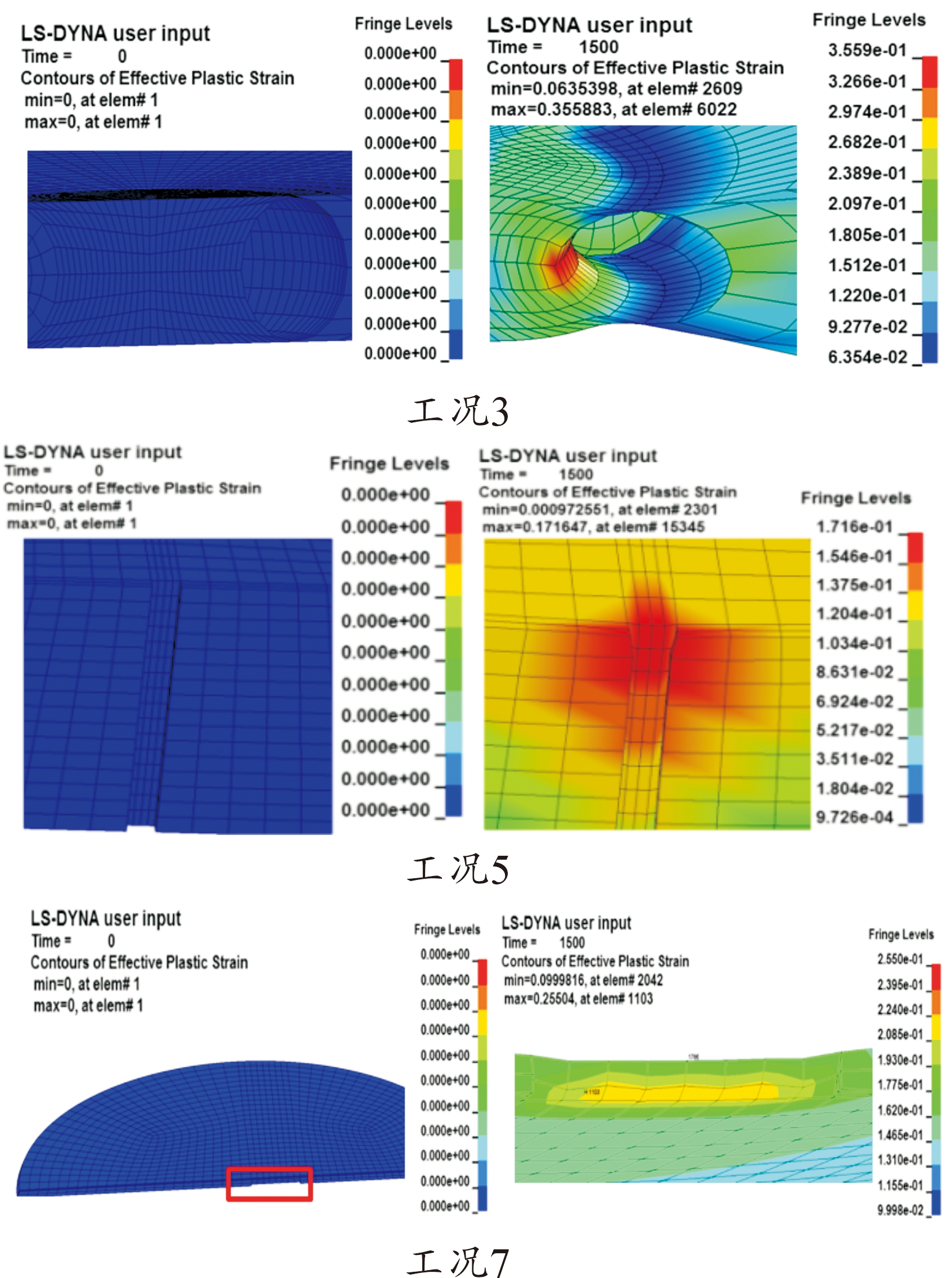
图2 部分工况裂纹缺陷的有效塑性应变云图
图3、图4、图5分别给出了图2中含裂纹缺陷的侵爆战斗部缺陷处发生较大塑性变形的装药单元(工况三、五、七)的应力-时间曲线、塑性应变-时间曲线以及温度-时间曲线。
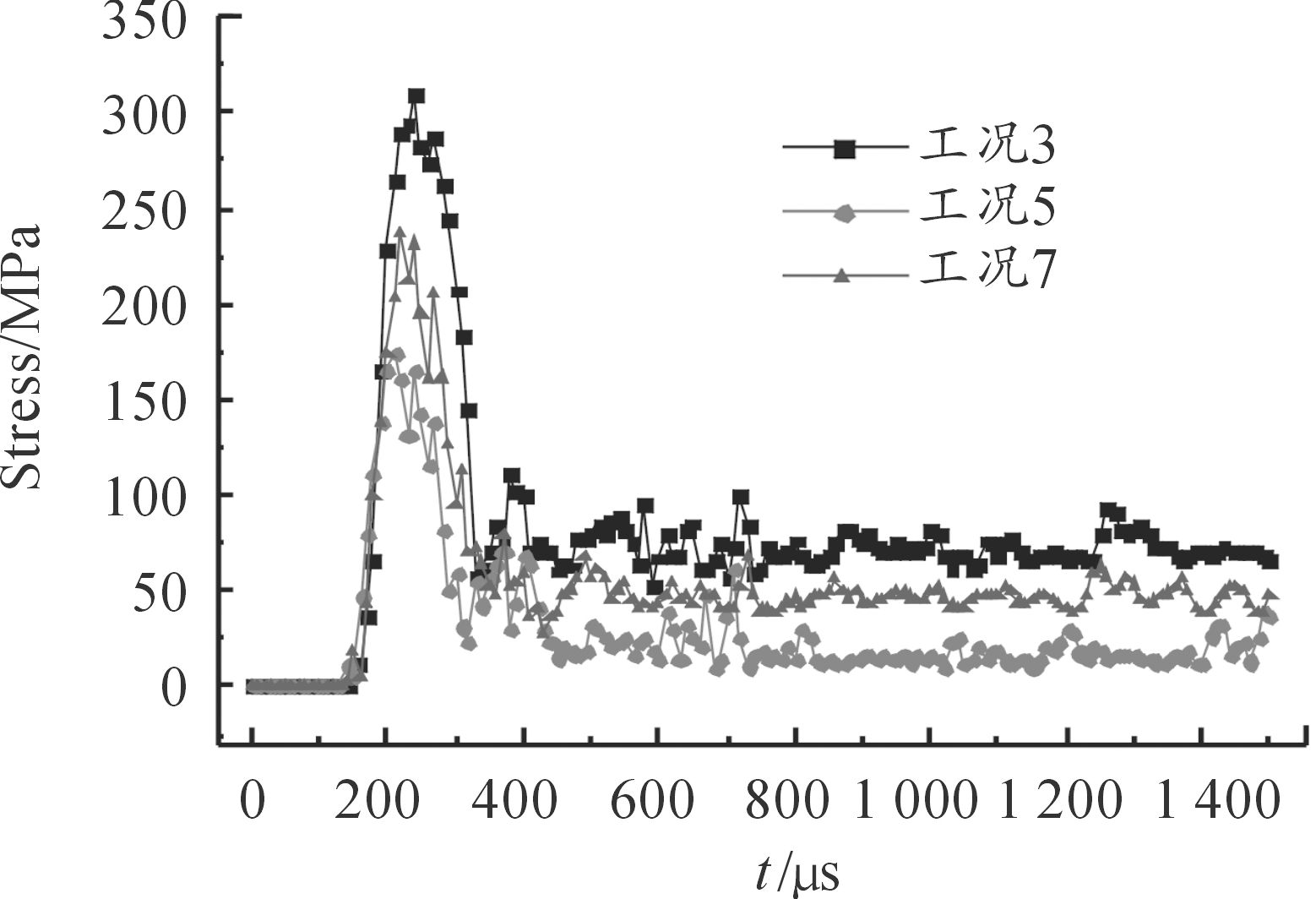
图3 部分工况下裂纹缺陷发生最大塑性应变单元的应力-时间曲线
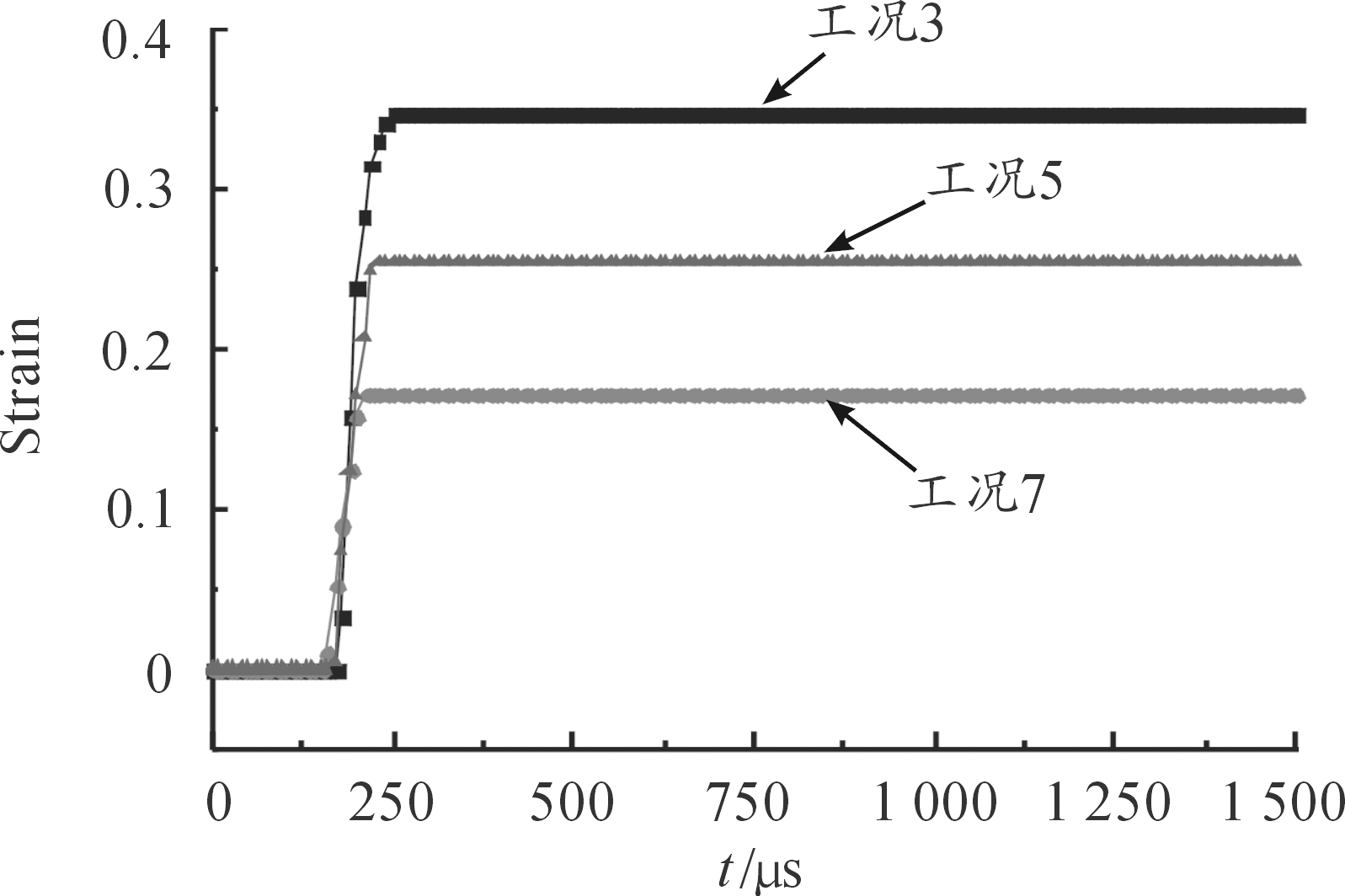
图4 部分工况下裂纹缺陷缺陷发生最大塑性应变单元的有效塑性应变-时间曲线
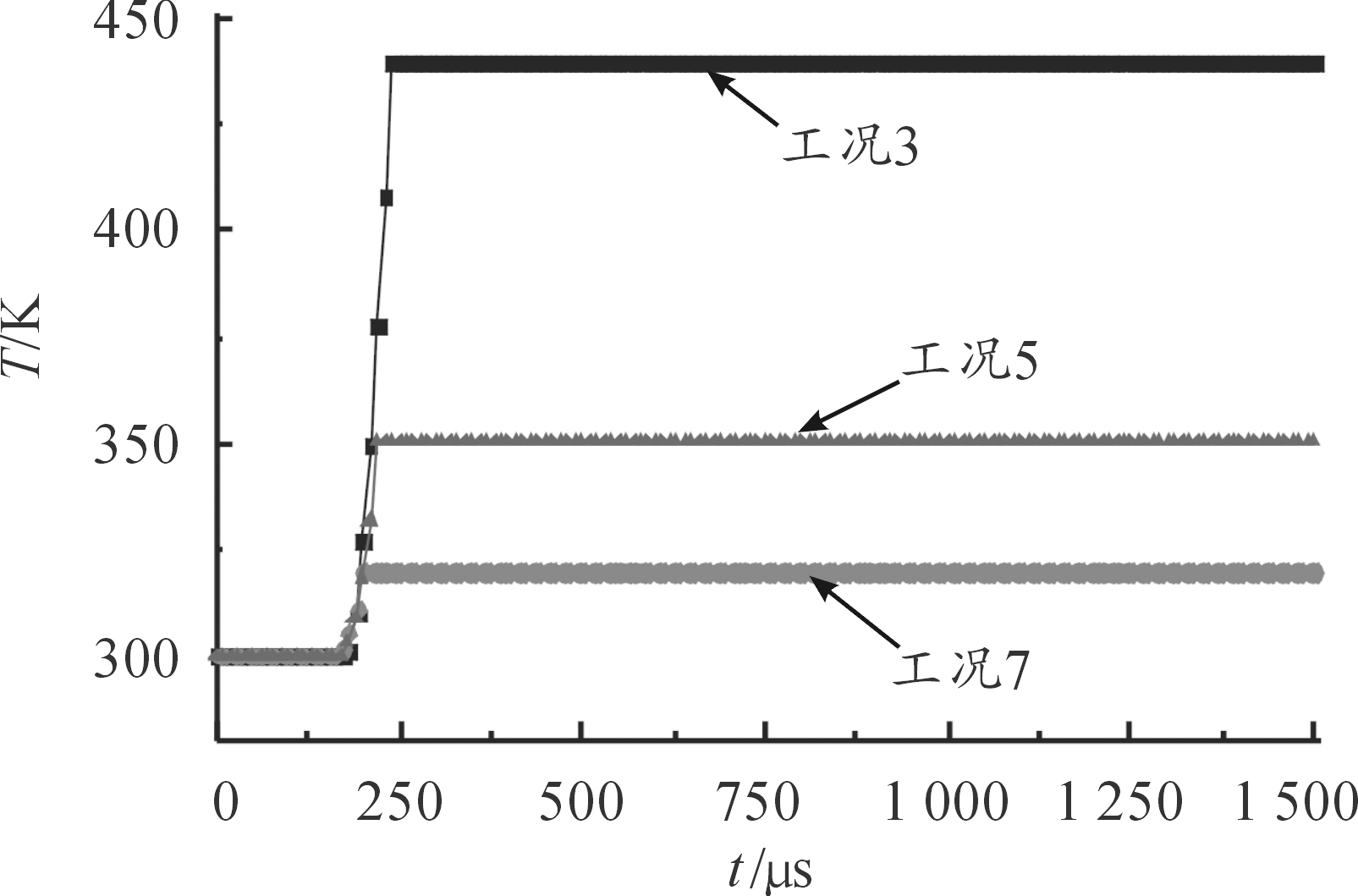
图5 部分工况下裂纹缺陷发生最大塑性应变单元的温度-时间曲线
从图3可以看出,处于同一轴向高度位置的裂纹缺陷,不同的裂纹缺陷形状对于侵爆战斗部穿甲过程中传进内部装药中应力波的响应在趋势上比较相似,但是在数值上存在较大差别,例如圆柱状裂纹缺陷的装药单元所承受的应力峰值就比三棱柱状裂纹缺陷装药单元的高一倍左右,四棱柱状裂纹缺陷居中,这既可能与装药缺陷的形状有关,也可能有裂纹缺陷所处的姿态状态的贡献。从图4可以看出,在同一轴向高度的位置上,工况三所代表的呈环形圆柱状裂纹缺陷的缺陷表面应力波作用下,发生的塑性应变最大,其次是正三棱柱,最小的是正四棱柱状裂纹缺陷。综合图4、图5可以看出:不同形状的裂纹装药缺陷形成的塑性应变对于缺陷处装药温升的变化与塑性应变的大小呈正相关性,并且塑性应变越大,使得裂纹缺陷处装药单元的温度上升值越大。
从图5可以看出,该侵爆战斗部在上述条件侵彻靶板过程中,处于550 mm圆柱状的裂纹缺陷处装药单元因塑性应变能的累积和装药的自反应放热引起的温升最大,达439.82 K(该侵爆战斗部主装药的5s滞期爆发点为533 K[2]),此外,根据非均质炸药在冲击载荷动态响应常用的点火判据为:
Pnt=constant
(2)
式(2)中: P为非均质炸药所承受的冲击应力; t为冲击应力作用在非均质炸药上的时间constant为常数,其值由炸药自身决定。
覃金贵博士[11]通过实验和数值模拟研究得出含铝PBX炸药JHL-3的点火判据常数为 P1.9t=4.3×107 MPa1.9·μs,而在含裂纹缺陷的侵爆战斗部主装药在穿甲过程中所承受的冲击应力根据图3中装药单元承受的应力-时间曲线进行计算,按上述判据计算的结果为1.54×107 MPa1.9·μs。根据以上计算结果可以得出:该状态下侵爆战斗部主装药比较安定,可能会发生燃烧,但是没有发生早炸的风险。
3.2 基于极差分析法的裂纹缺陷各因素对侵爆战斗部穿甲过程装药安定性分析
为了得出裂纹装药缺陷四个因素对于侵爆战斗部穿甲过程中装药安定性的影响主次,将前面利用L9(34)正交试验表设计得到的数值模拟结果按照极差分析数据表进行记录、整理,如表4所示。
表4 不同因素对于裂纹缺陷装药温度影响极差分析表
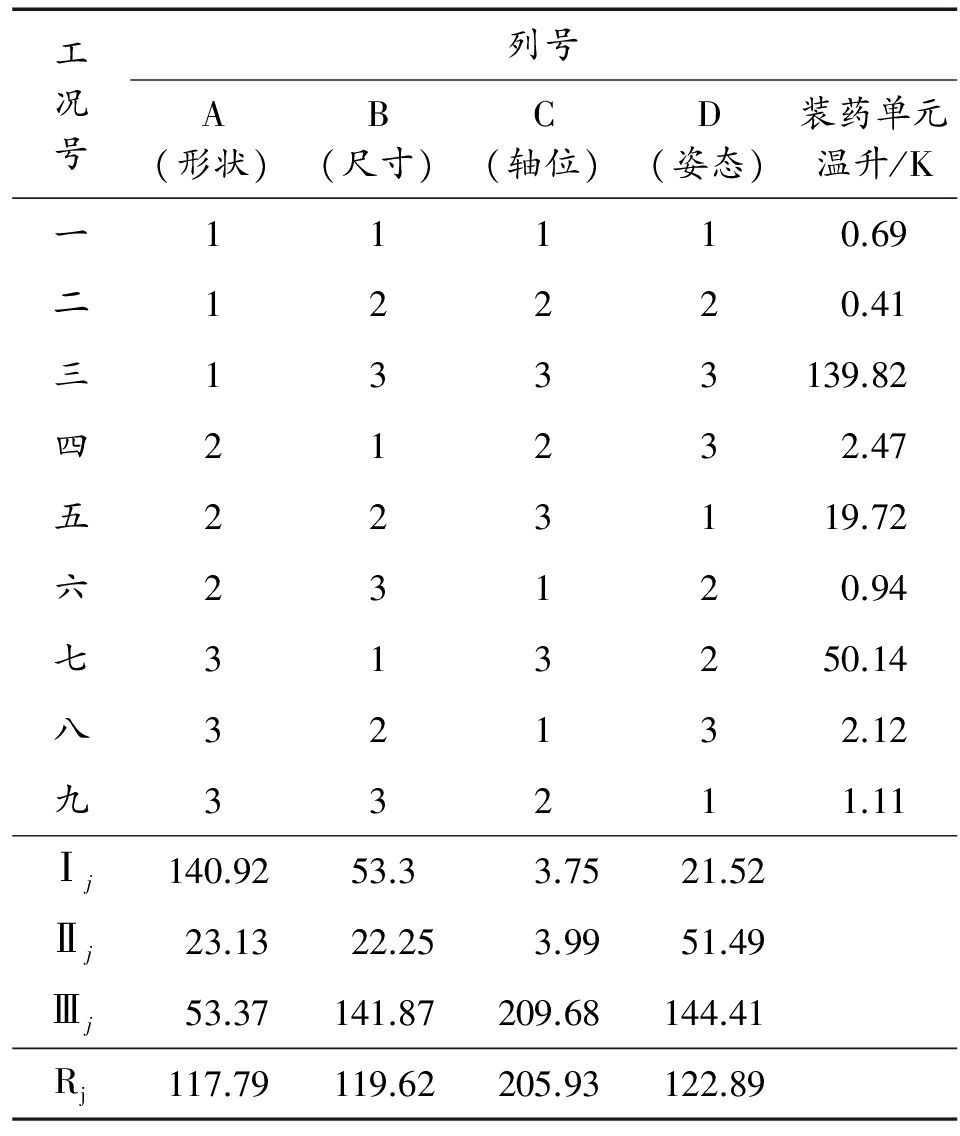
注:表中1、2、3分别代表不同因素的三个水平
表4为根据前面的工况设计进行数值模拟得到裂纹缺陷处装药单元温升数据的汇总和极差分析处理。可以发现:Rj行中C所代表的轴向位置这一栏的数据较大,A、B、D三列数据基本一致且A所代表的形状栏最小,这表明当裂纹缺陷的轴向位置这个因素的水平发生变动时,侵爆战斗部裂纹缺陷处装药单元的穿甲过程中温升变化较大,即轴向位置对于含裂纹缺陷的侵爆战斗部在穿甲过程装药安定性的影响最大,裂纹缺陷其他三个因素对侵爆战斗部装药的侵彻安定性的影响相对有限。
正交试验下裂纹缺陷的因素-指标图(装药单元温升)如图6,图6中A1、A2、A3分别表示的是裂纹缺陷形状因素的三个水平,可以发现:(1)裂纹缺陷为圆柱时,装药单元温升最明显,正三棱柱次之,正四棱柱温升最小;(2)裂纹缺陷的尺寸为10/80 mm时,装药单元温升最明显,2/16 mm较小,4/32 mm温升最小;(3)裂纹缺陷的轴向位置为550 mm时,装药单元温升最明显,337.5 mm和112.5 mm温升较小且基本相等;(4)裂纹缺陷的姿态为周向时,装药单元温升最明显,水平状态次之,竖直状态时温升最小。
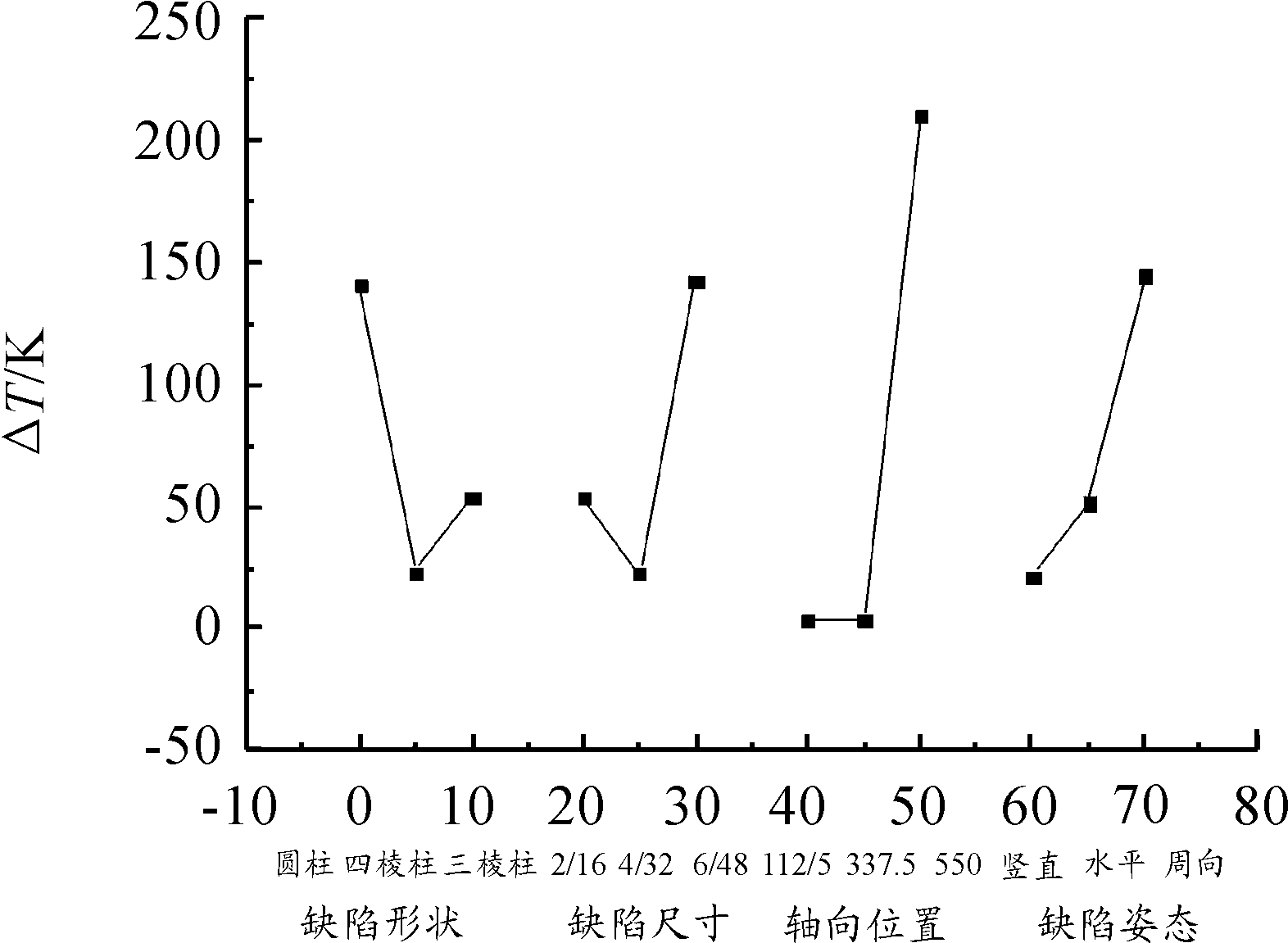
图6 正交试验下裂纹缺陷的因素-指标图
4 结论
1) 含裂纹缺陷的侵爆战斗部在侵彻靶板过程中,含裂纹缺陷的装药区域易形成较大塑性应变,且裂纹缺陷所处的轴向位置越高,缺陷处装药的有效塑性应变也同步变大,装药的塑性应变能引起的装药局部温升就越大。
2) 关于裂纹缺陷的四个因素对于侵爆战斗部垂直穿甲过程中装药安定性的影响,以裂纹缺陷的轴向高度对装药安定性影响最大,裂纹缺陷姿态的影响次之,裂纹缺陷模拟形状和尺寸的影响较小。
3) 几种因素作用下的裂纹缺陷的侵爆战斗部在以1.5倍音速穿甲过程中内部装药的裂纹缺陷并未闭合,因塑性应变能引起的装药的局部温升比较有限,对于侵爆战斗部装药的侵彻安定性的影响比较小。
参考文献:
[1] 尹俊婷,罗颖格,陈智群,等.一种弹药PBX装药的贮存老化机理及安全性[J].含能材料,2015,23(11):1051-1054.
[2] 赵勇华,陈霜艳,李国兰,等.侵彻战斗部装药安定性计算方法与探讨[C]//含能材料与钝感弹药技术学术研讨会.2014:143-147.
[3] 王洪波,王旗华,卢永刚,等.PBX炸药细观孔洞缺陷对其冲击点火特性的影响[J].火炸药学报,2015,38(5):31-36.
[4] 刘群,陈朗,伍俊英,等.PBX炸药细观结构冲击点火的二维数值模拟[J].火炸药学报,2011,34(6):10-16.
[5] 王晨,陈朗,刘群,等.多组分PBX炸药细观结构冲击点火数值模拟[J].爆炸与冲击,2014,34(2):167-173.
[6] 尚海林,赵 锋,王文强,等.冲击作用下炸药热点形成的3维离散元模拟[J].爆炸与冲击,2010,30(2):131-137.
[7] 温丽晶,段卓平,张震宇等.弹粘塑性双球壳塌缩热点反应模型[J].高压物理学报,2011,25(6):493-499.
[8] 焦志刚,郭秋萍,刘宗超.半穿甲弹侵彻过程中装药安定性数值模拟[J].弹箭与制导学报,2012,32(2):92-94.
[9] 陈丁丁,卢芳云,林玉亮,等.某含铝PBX压缩性能的应变率与温度效应[J].高压物理学报,2013,27(3):361-366.
[10] 陈全科,蓝林钢,路中华,等.含预制缺陷PBX炸药裂纹扩展过程的实验研究[J].兵器装备工程学报,2017(1):134-136.
[11] 覃金贵.PBX炸药非冲击点火机制试验和数值模拟研究[D].长沙:国防科学技术大学,2014.10.
[12] 李尚昆,黄西城,王鹏飞.高聚物黏结炸药的力学性能研究进展[J].火炸药学报,2016,39(4):1-8.