____________________________________________________________________________________________________________________________________
用格式:杨昭,王海云,姚春臣,等.热强钛合金管形件壳体的锻造成形试验研究[J].兵器装备工程学报,2017(12):301-304.
Citation formatYANG Zhao, WANG Haiyun, YAO Chunchen, et al.Study on the Forging Process of Hot-Strength Titanium Alloy Pipe-Shaped Part[J].Journal of Ordnance Equipment Engineering,2017(12):301-304.
____________________________________________________________________________________________________________________________________
作者简介:杨昭(1981—),男,硕士,工程师,主要从事弹箭工程技术及质量检测技术研究。
____________________________________________________________________________________________________________________________________
热强钛合金管形件壳体的锻造成形试验研究
摘要:对TC9和TC11钛合金壳体反复进行了β相区锻造与α+β双相区锻造相结合的复合锻造工艺试验,结果表明,热强钛合金管形件壳体可以通过制坯、扩孔、拔长、整形的工艺过程实现锻造成形,减小切削加工余量和加工难度,减少原材料的消耗。
关键词:热强钛合金;管形件;壳体;锻造;热处理
中图分类号:TJ76;TG319 文献标识码:A 文章编号:2096-2304(2017)12-0301-04
Study on the Forging Process of Hot-Strength Titanium AlloyPipe-Shaped Part
Abstract: The composite forging method of β phase and α+β double phase was tested on the manufacture of TC9 and TC11 hot-strength titanium alloy case. Results show that the forming process of titanium alloy shell can be forged through the process of billet, reaming, drawing, shaping. And the chipping allowanced and the raw material consumption are reduced.
Key words: hot-strength titanium alloy; pipe-shaped part; case; forging; heat treatment
某系列产品的管形件壳体要求强度高、质量轻、耐高温、耐腐蚀。而钛合金具有密度小、比强度高、耐蚀性好、耐热性优良等特点[1]。其中TC9合金在室温下的抗拉强度Rm不小于1 060 MPa,在500℃时的抗拉强度Rm不小于785 MPa;TC11钛合金在室温下的抗拉强度Rm不小于1 030 MPa,在500℃时的抗拉强度Rm不小于685 MPa[2]。这2种钛合金都属于α+β型 [3]的热强钛合金,所以被选定为该系列产品管形件壳体的材料。由于TC9和TC11钛合金的高温强度高,钛合金材料厂制造这种热强钛合金管材的难度很大,所以过去很长一段时间,材料厂不能供应TC9和TC11钛合金管料,TC9和TC11钛合金管形件只能采用棒料切削加工,切削加工余量大,加工较困难,材料利用率很低,生产成本高。为了减少原材料的消耗,降低生产成本,节约国家有限的钛资源,进行了TC9和TC11钛合金管形件壳体的制造工艺试验。
1 试验方案的优选
1.1 前期对管形件壳体成形方案的探讨
江南工业集团在钢铁件、铝合金件的铸造成形、锻造成形、挤压成形方面具有丰富的工作经验,对矩形、圆柱形钛合金件的锻造也有丰富的工作经验,但对于长径比为5的钛合金管形件的铸造、锻造和挤压没有先例。
首先考虑精密铸造工艺。但由于当时壳体的产量很少,钛合金精密铸造的过程也较复杂[4],需采用真空熔炼炉,还需对铸件进行热等静压处理等等 [5],搞精密铸造在经济上并不合算,所以尚未实施。
然后又考虑壳体的热挤压成形。但因上述壳体的长径比为5,挤压难度相当大。
在上述壳体批产之后,又考虑采用精密铸造成形方案。但由于铸造件的强度不能保证每批壳体都能达到产品图的要求,设计单位不同意,所以仍然未能采用精密铸造方案。
考虑到江南工业集团具有钛合金矩形件、圆形件锻造的设备条件和工作经验,其锻件已应用于了有关军工产品和神舟飞船,所以决定利用该厂的设备条件对这种管形件壳体进行锻造成形工艺试验。
检索有关热强钛合金锻造成形的资料,航空发动机盘形锻件和叶片锻造的文献较多,但管形件锻造的文献没有查到。可见这种管形件锻造没有先例,其难度是相当大的。
1.2 锻造试验方案
管形件壳体制造工艺改进试验的总方案是先采用TC9或TC11钛合金棒料下料,制坯,锻造成形,再经过热处理改善组织和消除应力,使其组织和性能符合产品要求,然后再经精密切削加工及质量考核检验而成为成品零件。
经对四种不同的锻造成形方案的比较,最后确定采用先对坯料预钻导引孔、再经锻压扩孔、拔长和整形三道工序锻造成形的试验方案。其始锻温度按有关资料[6]和江南工业集团的经验取960~970 ℃,终锻温度为850 ℃。
此锻造方案的优点是不需要复杂笨重的挤压锻造模具,所需的模具和工具比较简单,与现有的锻造设备条件相适应。与其它方案相比较而言,这种锻造工艺方法较简单易行。
计划在锻造出管形件壳体毛坯后,再对其进行热处理工艺试验。根据资料[7]、有关工艺标准[8]和江南工业集团的钛合金热处理经验,锻件的热处理采用双重退火工艺。
2 第1阶段的工艺试验
2.1 试验前准备
首先,按照试验方案制造锻造用的模具和工具。并且按试验方案进行原材料下料和钻孔,制备了5件试验用TC9钛合金坯料。
锻造坯料加热和锻件热处理用的加热炉都按照有关标准[9]的要求重新进行了检定,其炉温均匀度等项检测结果均符合有关标准对钛合金加热设备的要求。
2.2 锻造试验
第1阶段的锻造试验共进行了4次。锻造试验都在江南工业集团的锻造车间进行。
第1次试验是探讨TC9高强度钛合金锻造扩孔的工艺性和坯料尺寸的适应性。结果第1件扩孔只扩了一端,其坯料就开裂了。我们对其进行检查,发现另一头尚未扩孔处也有少量的纵向裂纹。由此,根据以往锻造神舟飞船用钛合金锻件的经验判断,其原材料的表皮可能存在氢氧氮污染层,表层还有可能存在裂纹缺陷,原材料缺陷是导致扩孔开裂的重要原因之一。
于是,取了2件未锻的坯料送机加分厂车除外圆上的材料表层。这2件坯料的外圆表层车去0.75 mm深后,发现其中1件坯料的外圆上有纵向裂纹。将有裂纹坯料的外圆再车去0.75 mm深后,发现其裂纹还有很深(见图1),只得将其剔除报废。
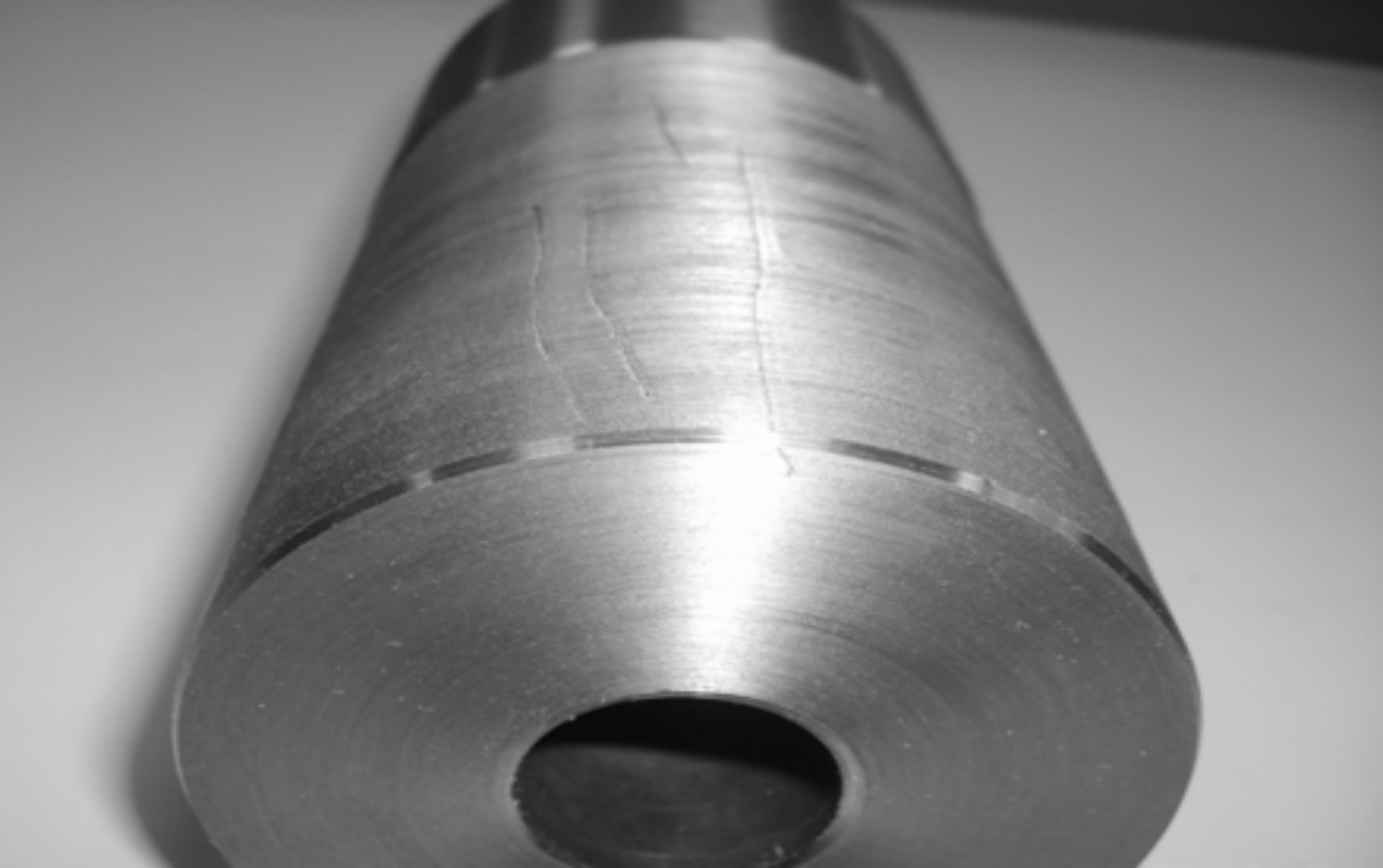
图1 锻造前有裂纹缺陷的坯料
此外,TC9钛合金含有1.8~2.8%的Sn元素,这也可能是其锻造极易开裂的另一个原因。所以锻造时应注意提高材料的成形性,减少坯料塑性成形的变形量。
第2次试验是继续探讨TC9高强度钛合金锻造扩孔的工艺性和坯料尺寸的适应性。这次试验,将坯料加热温度由960 ℃提高到了1 000 ℃左右,以提高材料的成形性。这次在锻第1件时,锥形冲子锻压入坯料孔中之后,工件虽然未裂,但再用平头冲子将锥形冲子退出坯料时,平冲子打弯了,锥冲子也没退出来。说明其钢制冲子的强度不够。
于是,在进行第3次锻造试验时,采取了以下改进措施:
1) 将坯料的预钻内孔适当增大。
2) 将冲子的直径加粗。
3) 冲子以及其它工具的材料由普通工具钢或结构钢改为采用热作模具钢。
4) 适当提高坯料加热温度。即采取β相区或临界区锻造。
采取上述措施后,第3次试验获得了扩孔的成功。
第4次试验主要是探讨钛合金管形件的拔长和整形。在拔长和整形时,随着长度的增加和壁厚的减薄,其材料越来越难以锻造,即出现了“打不动”的情况。于是,我们不得不又将锻造温度提高到1 000 ℃左右,锻出了3件尺寸符合要求的管形件壳体锻件毛坯(见图2)。
2.3 取样
锻造后,随机抽取了1件锻件由机加分厂切取加工了力学性能试样毛坯和金相试样毛坯。然后将一部分金相试样毛坯不热处理,其余试样毛坯均随同另外2件锻件一起进行热处理。
2.4 热处理试验
热处理试验在江南集团的热表处理分厂进行。根据试验方案,对上述管形件壳体锻件毛坯进行了双重退火。其中高温退火温度为930~950 ℃,低温退火温度为520~540 ℃。
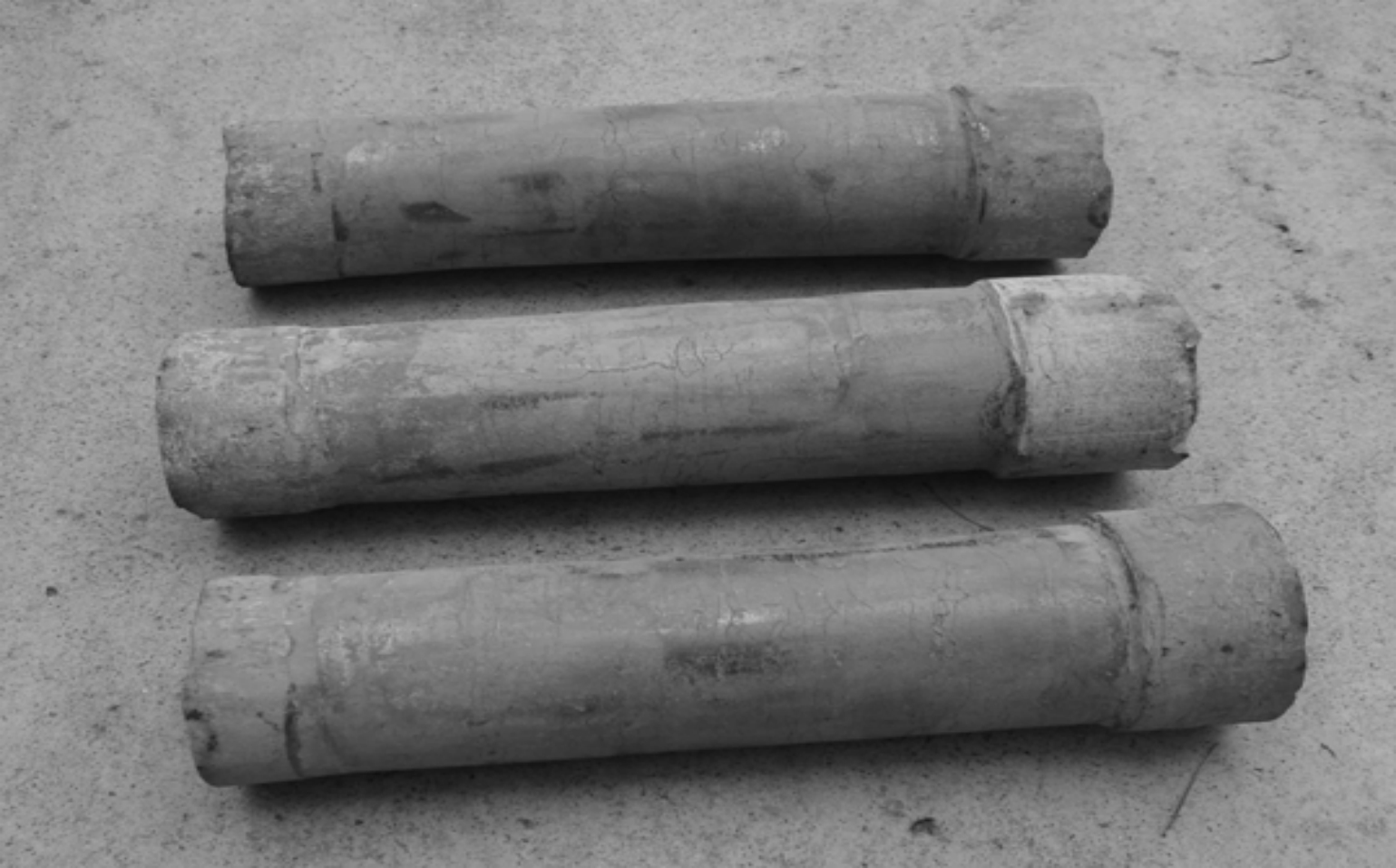
图2 首次锻造出的管形件壳体毛坯
2.5 试样加工及检验
试样毛坯加工成试样之后,由兵器工业中南地区理化检测中心检测了锻件热处理后的力学性能。其检测结果见表1。国标GB/T2965[2]的要求为Rm≥1 060 MPa,Rp0.2≥910 MPa,A≥9%。从表1可见力学性能符合国家有关标准的要求。
表1 TC9钛合金管形锻造试验件的力学性能
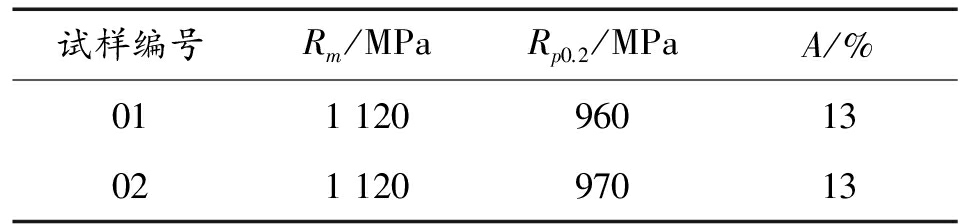
但是,未热处理的和已热处理的金相试样的检测结果都很不理想。不论是锻造状态的还是热处理状态的试样,其结果均为:“显微组织均存在完整原始β晶界,为魏氏体组织”。此结果不符合国军标GJB2218 [10]的要求。
根据资料[6]分析可知,金相组织不符合标准要求的原因是锻造温度偏高,超过了β转变温度,并且导致β晶粒长大。这就需要解决锻件成形需提高锻造温度而材料组织又需限制提高锻造温度的矛盾。
3 第2阶段的工艺试验
3.1 锻造试验
由于第1阶段工艺试验的金相组织不理想,所以又制备锻造用的坯料,进行了第2阶段的工艺试验。在第2阶段试验中作了一些改进。如,将坯料长度适当增长,以减少拔长和整形的难度。
为了解决锻件成形需提高锻造温度而材料组织又需限制提高锻造温度的矛盾,试采用了先高温锻造后常规锻造的锻造方法。即:在扩孔工序以及拔长工序的第1火,采用较高的温度锻造,以提高材料的成形性,防止锻件开裂;在拔长工序的后期以及在整形工序,降低锻件的加热温度或缩短加热时间,采用常规的α+β双相区锻造,以保证锻件的组织性能符合要求。
此外,在工件扩孔之后还作了不用模具而自由拔长的尝试,但由于自由拔长容易拔裂,所以后来还是采用专用模具进行拔长。
采用上述措施之后,锻件扩孔、拔长开裂、拔长锻打不动等问题均得到了解决。
3.2 热处理试验及检验
第2阶段锻成的管形件壳体毛坯的热处理仍然按照双重退火的热处理工艺进行。锻件经热处理后,抽样线切割金相试样检查金相组织。其组织中均无完整原始β晶界(见图3),符合国军标GJB 2218的要求。其材料组织的问题得到了解决。
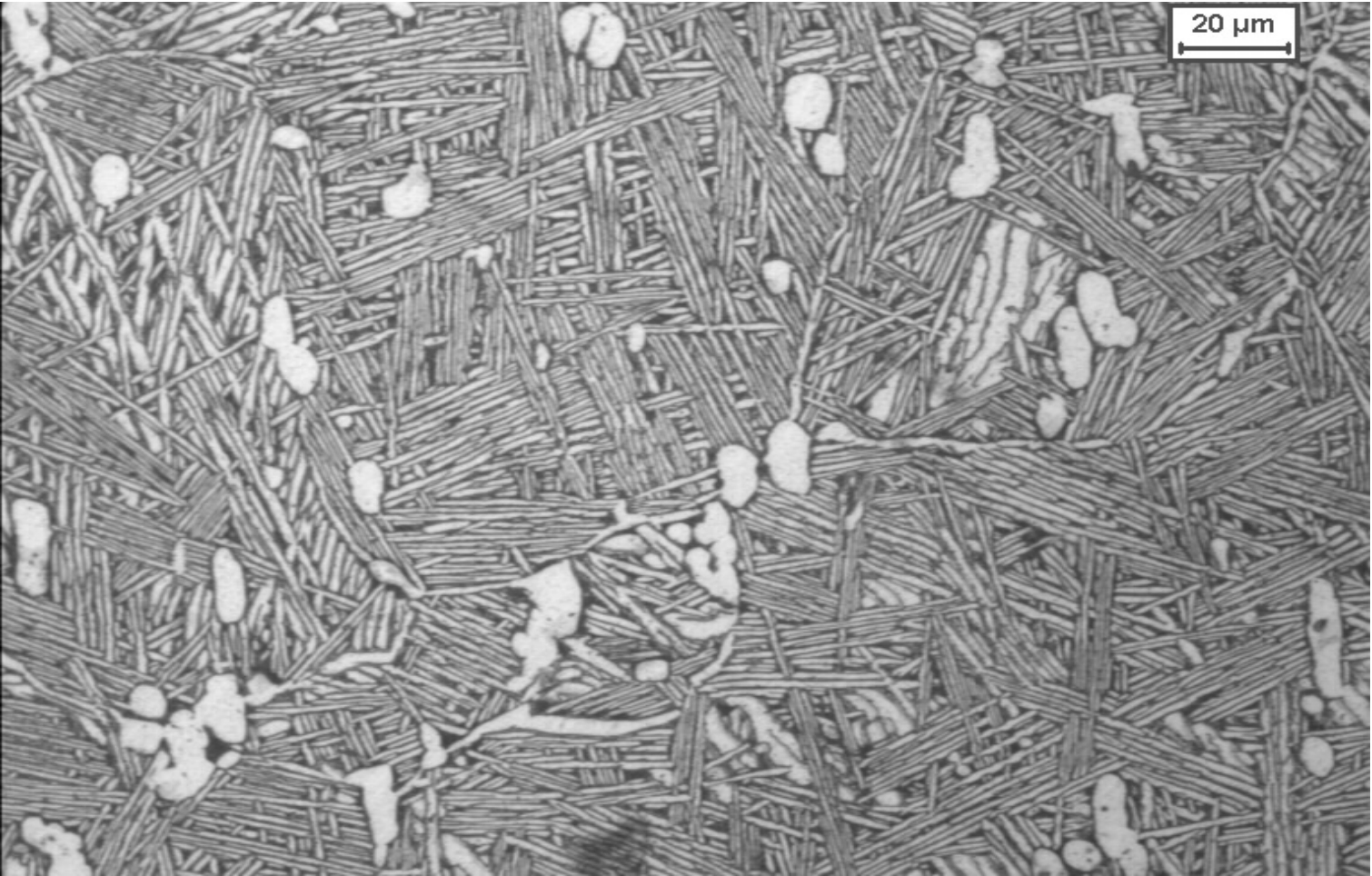
图3 壳体锻件的金相组织(双相组织)
4 后续的切削加工及应用试验
采用上述锻造方法锻造的管形件壳体毛坯经过尺寸、外观、力学性能、金相组织等项检验合格后,转入机加分厂进行了切削加工。切削加工成了壳体零件之后,进行了零件的尺寸、外观以及无损探伤等项质量检验。其各项检验的结果都符合产品质量要求。
首批试制的管形壳体锻造件经机械加工后的样件见图4。
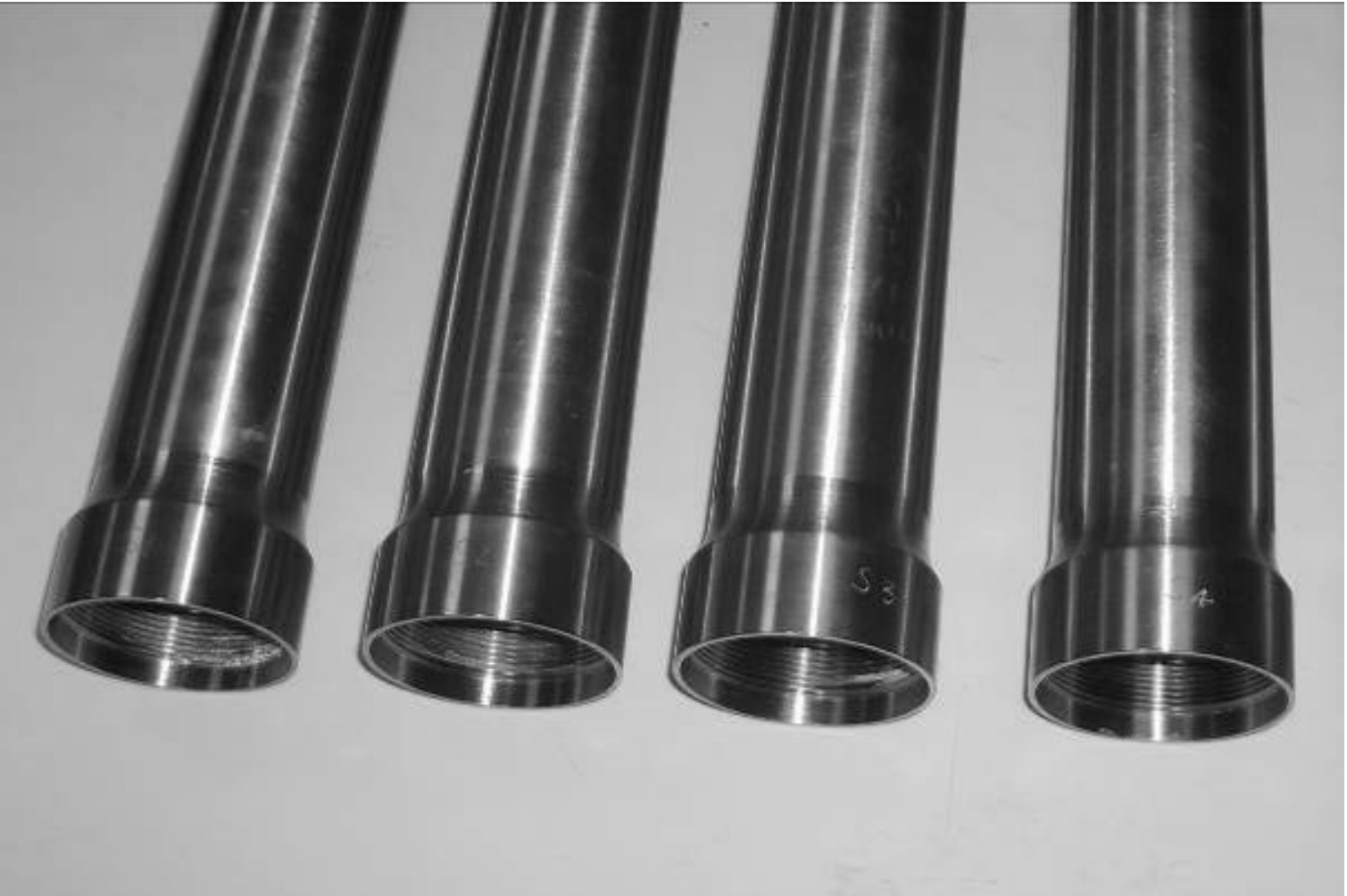
图4 管形壳体样件
后来又对TC11钛合金管形件壳体进行了锻造试验,证实此锻造方法对于TC11钛合金管形件壳体也适用。
上述锻造及热处理工艺方法获得了国家发明专利[11]。
5 技术关键
5.1 分步锻造是热强钛合金管件成形的有效途径
TC9和TC11热强钛合金在高温下的强度较高,存在成形难和模具强度不足的问题,采用锻模直接将热强钛合金棒料一次挤锻成管形件是很困难的。即使采用高温强度很高的价格昂贵的特殊材料制造锻模,也很困难。在本项工艺试验中没有采用这种直接挤锻成形的锻造方案。
而按照制坯、扩孔、拔长、整形的步骤分步进行锻造,可以降低材料成形的难度,而且可以采用较简单和易于冷却的模具,有利于解决模具高温强度不足的问题。本项工艺试验的结果证实,采用制坯、扩孔、拔长、整形的工艺过程进行分步锻造是热强钛合金管形件成形的有效途径。
5.2 合理采用β相区锻造方法
军工产品α+β型钛合金零件的锻造,一般要求在α+β双相区进行锻造,以确保锻件的组织和性能符合要求。但对于TC9和TC11热强钛合金管形件,按常规在α+β双相区锻造,材料的成形较困难,很容易产生裂纹。若提高温度在β相区锻造,则又会出现材料组织不合格的问题。
解决这一矛盾的方法就是采用β相区锻造与α+β双相区锻造相结合的复合锻造方法。即在扩孔工步以及拔长工步的前期,适当提高锻造温度,使其始锻温度略高于β转变温度;而在拔长工序的后期以及整形工序采用α+β双相区锻造。
本项试验的结果证实这种复合锻造方法可以同时解决上述材料高温强度高、难以成形和易开裂问题。
5.3 应注意提高锻模和工具的强度
在锻造试验前期,多次出现简易模具和工具不耐用的情况,将模具材料由普通模具钢改为热态下强度较高的热作模具钢之后,锻造才能正常进行。这说明,热强钛合金管形件锻造用的模具和工具应有足够的强度,不宜采用普通模具钢制造,在使用中注意对模具和工具的冷却,防止因温度偏高而使其材料的强度不足。
6 结论
1) 对于高温强度较高锻造难度大的TC9和TC11热强钛合金管形件,在长径比不大于5的情况下,可采用预制带孔坯料、锻压扩孔、拔长、整形的锻造工艺方法进行成形加工。经双重退火热处理后,成为组织性能符合我国军标要求的锻造毛坯。
2) TC9和TC11热强钛合金管形件壳体锻造时,宜采用β相区锻造与α+β双相区锻造相结合的复合锻造方法。
3) 热强钛合金管形件锻造用的模具和工具不宜采用普通热作模具钢制造,而应采用热态下强度较高的热作模具钢制造。
参考文献:
[1] 莫畏.钛的金属学和热处理[M].北京:冶金工业出版社,2014.
[2] GB/T 2965—2007, 钛及钛合金棒材[S].
[3] 才鸿年,赵宝荣.金属材料手册M].北京:化学工业出版社,2011.
[4] GJB 2896—1997, 钛及钛合金熔模精密铸造规范[S].
[5] 周彦邦.钛合金铸造概论[M].北京:航空工业出版社,2000.
[6] 中国机械工程学会锻压学会.锻压手册,第1卷,锻造[M].北京:机械工业出版社,1993.
[7] 中国机械工程学会热处理学会.热处理手册,第1卷工艺基础[M].第4版.北京:机械工业出版社,2008.
[8] GJB 3763A—2004, 钛及钛合金热处理[S].
[9] GJB 509B—2008, 热处理工艺质量控制[S].
[10] GJB 2218A—2008, 航空用钛及钛合金棒材和锻坯规范 [S].
[11] 王海云,姚春臣,王德明,等.一种钛合金管形件锻造成型工艺方法[P].中国: ZL2013 1 0317421.2, 2015-07-01.